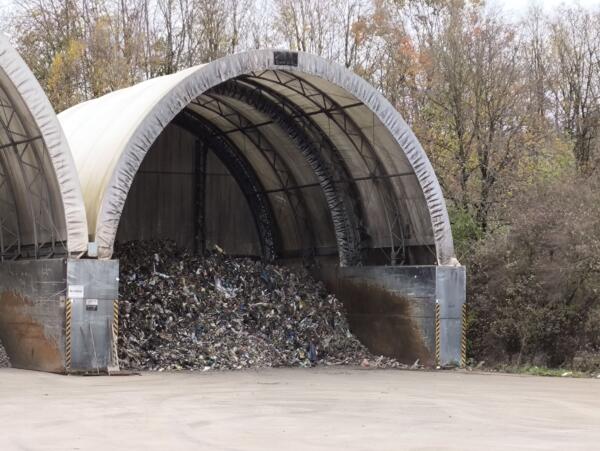
The Westerwald MBS plant serves as a treatment plant for regional household and household-type commercial waste. Included among several by-products is an ecological secondary fuel for power and cement plants, known as dry stabilate. Right from the outset, the company has relied on a robust and reliable complete system comprising conveyor technology and pre- and post-shredding from Vecoplan. As part of a general overhaul, one of the Vecoplan shredders was successfully replaced after 16 years.
“High performance, powerful and reliable: these are the essential qualities we look for in our machine technology – and the machines must also be robust and safe. You’ll not find laboratory conditions here – but you will see a very demanding working day,” says Matthias Baldus, Managing Director of the MBS plant Westerwald GmbH & Co. KG in Rennerod, a small town in Rhineland-Palatinate between Limburg an der Lahn and Siegen. “Weprocess up to 92,000 tonnes of residual waste from the Westerwald and Limburg-Weilburg districts.” MBS? “It stands for mechanical-biological stabilisation process. We don’t just get rid of waste,” says Baldus. “It’s the raw material of the future. We’re committed to environmentally friendly and resource-efficient waste recycling. That’s why we use state-of-the-art processes to separate the different types of waste – and recover the raw materials they contain.” The company currently employs 18 experienced staff.
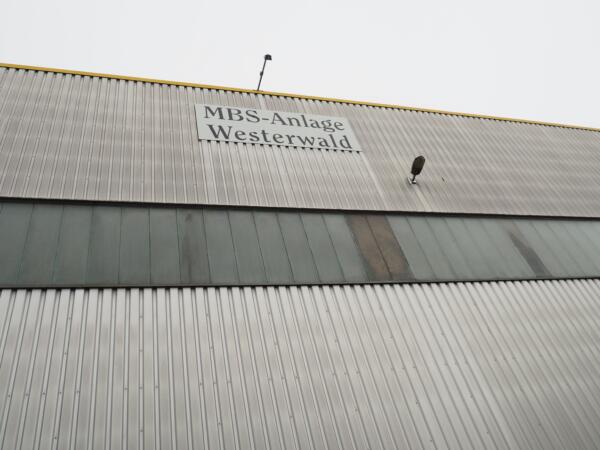
The plant has been in operation since the beginning of 2000 and is owned by the Westerwald and Limburg-Weilburg districts. Herhof Umwelttechnik was responsible for the planning, design, construction and commissioning of the plant. Vecoplan AG from Bad Marienberg (just 16 kilometres from Rennerod) was commissioned by the company as its main supplier for mechanical processing technology. Vecoplan develops and manufactures machines and plants which, among other diverse tasks, can process and treat alternative fuels from household and commercial waste – in other words, waste-to-energy. The machine and plant manufacturer now employs around 600 people worldwide. Vecoplan’s wide-ranging machine product portfolio services include consultancy, finding effective solutions and detailed planning. Its integrated project management covers installation, commissioning and comprehensive service. Backed by its many years of expertise in project development for the processing and recycling of waste, plastics, wood and biomass, the company provides an all-round support service for its customers.
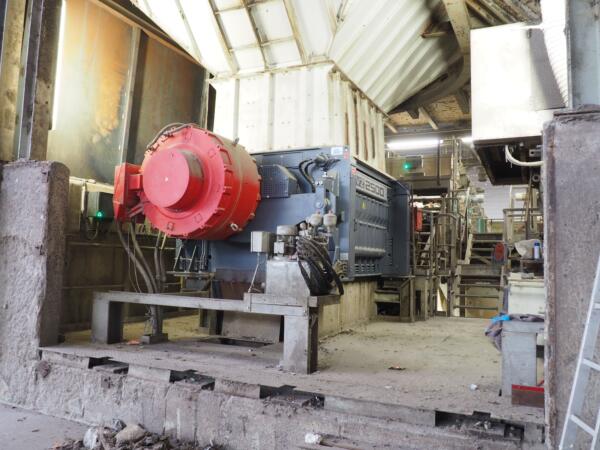
Efficient shredding
“In Rennerod, we’ve implemented a high-performance, two-stage shredding process that shreds the different and often challenging materials into a homogeneous output,” says Steffen Heimann, Sales Area Manager at Vecoplan. Up to 400 tonnes of unsorted and untreated waste from municipal collections and private disposal companies are transported to the plant every day. The delivered waste is collected in a deep bunker and fed to the pre-shredder by an automatically-operated crane.
“We’ve been using two Vecoplan VVZ 2500 series twin-shaft shredders since 2008,” says José Fialho, Operations Manager at MBS. The effective high-performance cutting unit consists of two armoured, solid steel rotors with intelligently arranged, bolted knives and replaceable counter knives, ensuring a high-powered and extremely effective shredding performance. These features make the shredders ideal for these difficult-to-process materials. “The machines take in the moist input which has a maximum size of up to 1,500 millimetres and process it into a homogeneous output with a maximum size of 200 millimetres,” explains Fialho. A detection system protects the machine from solid extraneous materials such as metal items. The machine is easily accessible via two hydraulic maintenance doors, and extraneous materials can be simply removed with no risk of long downtimes. “We look at the pre-shredders every week and turn or change the cutting tools if at all necessary,” says Managing Director Baldus.
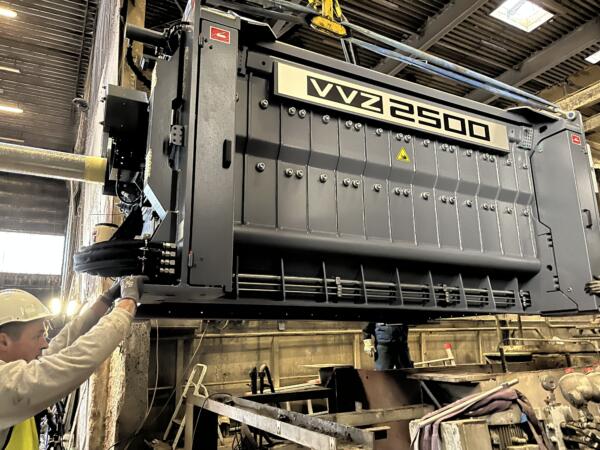
All-round renewal
In the autumn of 2024, Vecoplan successfully refurbished one of the two VVZ 2500s as part of a general overhaul – after sixteen years. The Vecoplan assembly specialists dismantled the components and completely rebuilt the machine. The highly reliable HiTorc, an energy-efficient electric direct drive developed by Vecoplan, was left in place. It has been replacing conventional drives for years. “The HiTorc works dynamically and has a strong start-up phase and a high torque,” says Baldus. It operates without any mechanical drive elements such as gears, belt drives, slip clutches and hydraulic motors. It’s not challenged at all by the sudden changes in load that occur when shredding waste. The water-cooled HiTorc drive is predestined for applications in dusty environments – and it’s virtually maintenance-free. Safety is also greatly enhanced as no flammable hydraulic oil is used. “Thanks to the direct mounting of the drive on the rotor shaft, there’s no loss of power in the drive train – that’s how the frequency-controlled HiTorc achieves its very high-efficiency level – with the lowest possible power consumption,” explains Heimann.
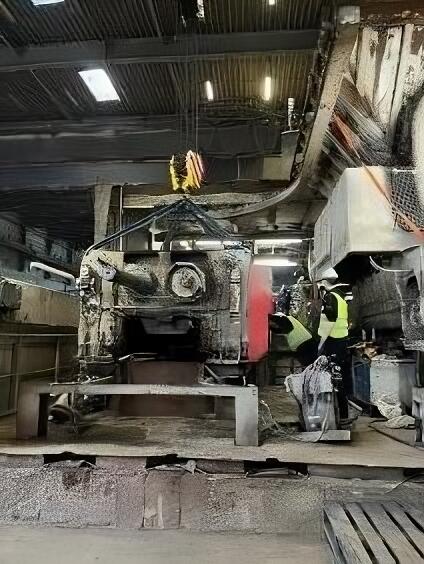
The perfect fuel
The shredded and moist material is transported by belt conveyor to an intermediate bunker. The conveyor is equipped with powerful overhead magnets which extract any metal materials en route to the bunker. An automated process crane then transports the homogenised mixture to concrete bunkers (the so-called rotting boxes) for biological drying. “We can only break down dry material mixtures into their valuable components by machine,” says Baldus.
After around one week, the process crane automatically picks up the dried waste mixture and feeds it into a ‘walking floor bunker’. From there, the mixture is conveyed to a drum screen and sieved down to 50 millimetres. The remaining coarse fraction – the so-called screen overflow – is then sent for secondary shredding. Vecoplan has installed two VNZ 2500 series machines to shred the material into a particle size of less than 50 millimetres. The VNZ series consists of reliable, twin-shaft secondary shredders with pneumatically pre-tensioned counter knives. The machines are not susceptible to faults and impress all users with their extremely high level of technical availability. They are also equipped with a profiled rotor for maximum cutting performance. The MBS plant benefits from homogeneous particle size distribution, long service life, low operating costs and optimal accessibility for maintenance. Before the shredding process takes place, a magnetic separator removes coarse ferrous particles from the mass. Also in full operation – a VEZ 2500. Specially designed for the production of substitute fuels, this machine shreds the material to a particle size smaller than 30 millimetres. “This system was retrofitted at MBS. It enables us to offer different fuel qualities to different power plants,” explains Steffen Heimann.o successivamente presso MBS per poter offrire differenti qualità di combustibile a diverse centrali elettriche” spiega Steffen Heimann.
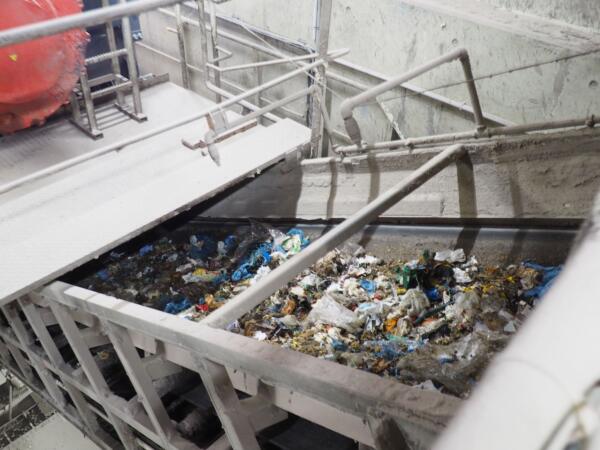
To separate heavy and light materials by density, a Vecoplan drag chain conveyor feeds the material to a heavy/light separator. Both light and heavy materials are separated from the ferrous and non-ferrous metals using magnetic separators and eddy current processes – and can be subsequently returned to the materials cycle.
“The light material is the dry stabilate,” explains José Fialho. “It consists almost entirely of combustible components and has almost twice the calorific value of undried brown coal.” The CHP plant in Witzenhausen, Hesse, for example, uses this ecological secondary fuel, which contains a high biogenic proportion, to supply a paper factory with electricity and steam. Every day, trucks loaded with around 200 tonnes of compacted dry stabilate leave the MBS plant en route to customers.
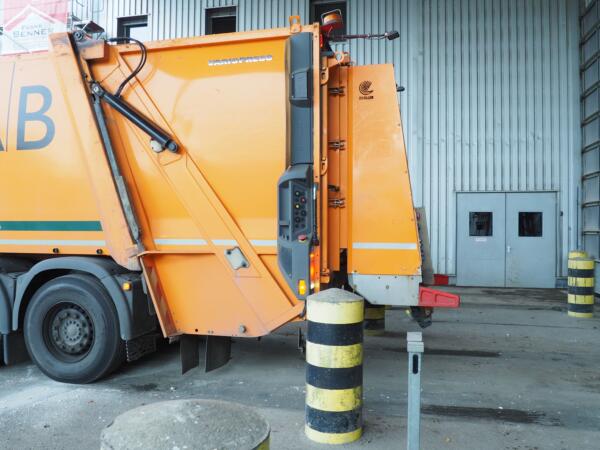
Partners within reach
“We not only appreciate Vecoplan’s reliable and consistently robust systems,” says Matthias Baldus. “The company also has the expertise to implement customised projects.” He is also very enthusiastic about the excellent cooperation between the two companies. Baldus: “We witnessed evidence of how outstanding this cooperation is yet again in the autumn, during the general overhaul of the pre-shredder – the assembly technicians performed their tasks very impressively – with minimum disruption and maximum proficiency.” This statement from the Managing Director underlines the hands-on mentality with which Vecoplan personnel tackle challenges and solve tasks pragmatically.