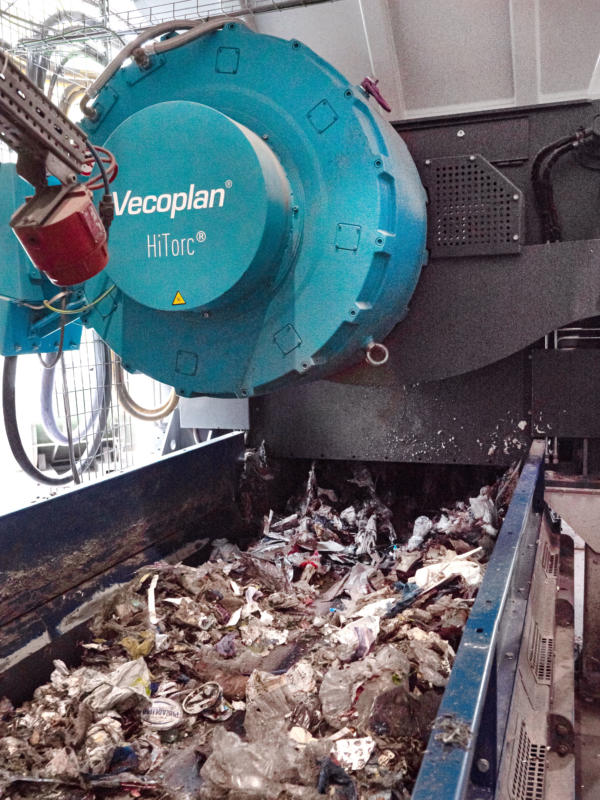
How does Vecoplan support its customers in making their production more carbon-neutral? One important lever here is energy efficiency – and that’s why the machine manufacturer equips its shredders with the proven HiTorc direct drive, among other advanced concepts. Why customers benefit from this powerful combination and what this all-electric solution entails is explained by Vecoplan’s Divisional Manager for Recycling | Waste, Martina Schmidt.
We don’t want to foresee the future; we want to make it possible. “This quote from Antoine de Saint-Exupéry matches our modern times and our strategy at Vecoplan perfectly,” explains Martina Schmidt. “After all, our goal is to find an efficient solution for processing every material in the primary and secondary raw materials industry – and to achieve this, we always have our eye on what tomorrow could bring.”
This was already the case 20 years ago. Customers required ever larger and more powerful shredders. This also had an impact on the drives used, because they had to be able to master the increased throughput and have sufficient torque to efficiently handle challenging input loads contaminated with extraneous materials. During this period, Vecoplan developed the HiTorc, which the company patented. A controller integrated in the frequency converter ensures that the best possible torque is available at the rotor shaft at all times and in all operating scenarios. This gives the synchronous motor a truly impressive degree of efficiency. Martina Schmidt: “Compared to other electromechanical drives, our customers can save up to 40 per cent energy with shredders that are equipped like this – and even up to 60 per cent compared to hydraulic drives. We can also demonstrate this fact clearly.”
Here is a cautious calculation using minimal data: Based on HiTorc drives with around 3,000 operating hours and approximately 15 years of use, all our Vecoplan customers together not only saved more than 200 million euros at an assumed electricity price of 0.10 euros per kilowatt hour but also produced more than one million tonnes of CO2 less than they would have with alternative drives. That’s the equivalent of about 122,000 households which get their energy from fossil fuels each year, almost 220,000 long-haul flights between North America and Europe – consisting of round trips during the same period – or the annual carbon dioxide intake of 40 million trees.
Shredder and drive – a powerful combination
“The HiTorc also requires very little maintenance because we don’t use mechanical drive elements like belt and gear drives, flywheels and clutches,” says Martina Schmidt. “In combination with our shredders, customers get solutions that are both reliable and resistant to extraneous materials – ideal for heavy-duty, continuous use.” During a project with a Vecoplan shredding solution for difficult materials, the operator only had to replace the HiTorc after 58,000 hours of operation – and the customer had only adhered to the usual maintenance intervals. The motor was neither overhauled nor repaired during its entire lifetime.
And because mechanical components are eliminated, the mass moments of inertia in the entire drive system are also significantly reduced. This means that the high availability of the torque enables a problem-free start-up under load, i.e., when the shredding area is full. The fully automated control system uses continuous speed analysis and electrical current evaluation to detect machine overload at an early stage in the ongoing shredding process. If extraneous material is encountered, the rotor shaft will stop in just a few milliseconds. This prevents damage to important components. After a short counter-rotation, the Vecoplan drive turns in the required direction again in a few seconds.
“In combination with the drive, we offer customers advanced shredding solutions to meet tomorrow’s needs. Our customers appreciate this, and that’s why we’re continuing to develop these technologies,” says Martina Schmidt. Besides the HiTorc drive with its high start-up power and torque, Vecoplan offers the equally energy-efficient and patented ESC drive with its patented belt technology.
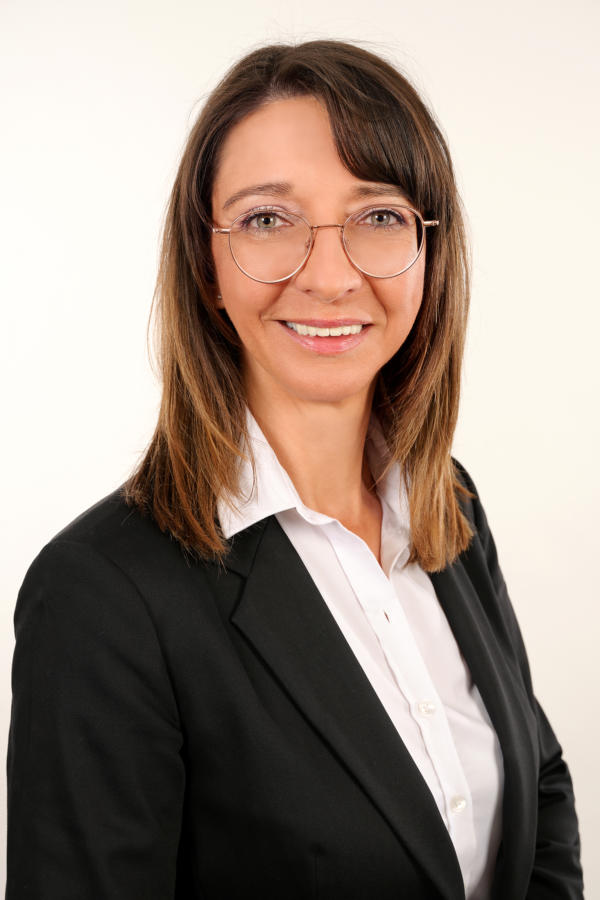
Martina Schmidt: “We always have our eye on what tomorrow could bring.”