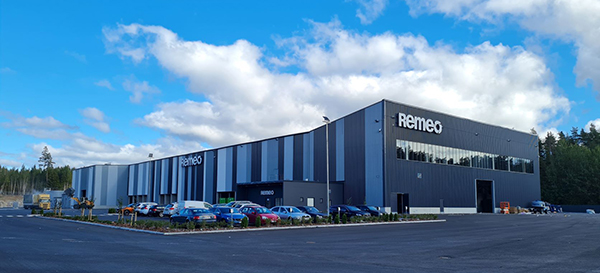
STADLER and ZenRobotics have built the pioneering new sorting plant with Remeo Oy, a Finnish company specializing in environmental management. STADLER designed the Materials Recovery Facility (MRF) in collaboration with Remeo and built it, while ZenRobotics supplied AI-based robotics waste sorting technologies. The facility, located in the Greater Helsinki Region in Finland, stands out not only for the state-of-the-art Artificial Intelligence (AI) technology, cutting-edge processes, and high level of automation, but also for integrating Commercial & Industrial (C&I) and Construction & Demolition (C&D) waste lines in the same plant – an industry first. The facility was completed ahead of schedule, despite the difficulties created by the Covid-19 pandemic – an achievement that is testament to the successful collaboration between Remeo, STADLER and ZenRobotics.
The new Remeo MRF was inaugurated on 14 February 2022 with a ribbon-cutting ceremony hosted by Remeo’s CEO Johan Mild and Business Director Mauri Lielahti. The Finnish Minister of Economic Affairs, Mika Lintillä cut the ribbon, declaring the facility officially open, and highlighted the significant leap forward that the innovative facility constitutes for the Finnish circular economy. A lights and music show symbolized the new era of circular economy in Finland and the innovations in this field. The event was livestreamed due to Covid-19 restrictions. The online audience also viewed footage of the facility’s construction and a virtual tour of the premises.
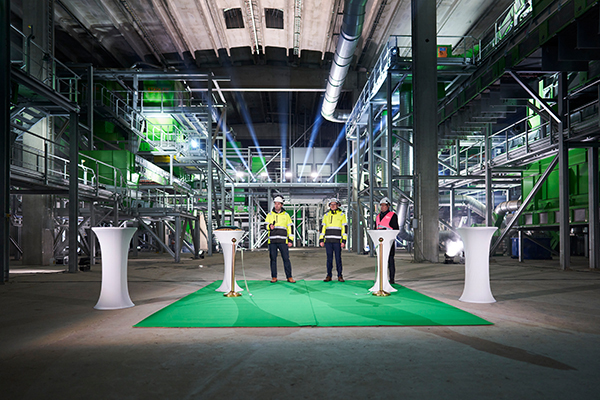
A unique design challenge: two plants in one, high automation
The new Remeo MRF presented unique and complex design challenges for being the first of its kind, combining a C&D plant capable of processing 30 t/h and a C&I plant with 15 t/h capacity, and its high level of automation. Resolving them required the best ingenuity and innovative thinking from Remeo, STADLER and ZenRobotics, as well as an exceptionally close collaboration among the partners.
“The combination of our experience with the C&D line, STADLER’s solid familiarity with the C&I line and ZenRobotics’ impressive knowledge of robotics made this an excellent co-operation with the best results,” Mauri Lielahti, Business Director, Processing at Remeo. “We appreciated STADLER’s capability to be innovative, their willingness to seek new solutions and that they were ready to listen to the customer’s needs. We have been working closely with ZenRobotics since 2014 and have a continuous development cooperation. Thanks to the knowledge we acquired on our older recycling facility, we knew what we should and should not do. It has been easy to work with them.”
The result of this collaboration is a design that “combines ballistic separators, screening drums, 3D drums, optical sorters, air separators, sorting robots, magnets, eddy-currents as well as the ZenRobotics robots, making it the most advanced waste sorting facility in the European Union,” says Nikolaus Hofmann, Sales Engineer at STADLER.
Juha Mieskonen, Head of Sales at ZenRobotics, adds: “The Remeo facility is equipped with 12 robot arms that pick objects from bulky C&D waste that weigh up to 30 kilograms and together perform up to 24,000 picks per hour. In other words, the robots do all the heavy lifting that’s neither safe nor feasible for humans. They sort multiple fractions on the spot, including different qualities of wood, metals, stone and plastic. The robots can be trained to recognize new fractions if needed, thanks to various sensors and artificial intelligence. The facility integrates two different processing lines and features two consecutive robot systems on each line. It’s the largest fully roboticized MRF of its kind, which brought new operations and safety aspects to take into consideration in the design.”
“The most innovative aspects of the design can be described with the ‘Form from Function’ principle,” explains Nikolaus Hofmann. “The function of the lines was the driver in every design decision. For example, C&D waste tends to clog, especially at 90-degree transitions of the conveyors, so we eliminated them in the design as much as possible. To accommodate this, we designed a narrow and long building rather than a square structure.”
This approach to design extended to looking at the best solutions for maintenance, “in order to ensure a reliable and safe sorting facility for the future,” says Nikolaus Hofmann. “The layout is designed for easy maintenance, with almost every motor being accessible from walkways and maintenance platforms. The layout groups similar equipment together where possible and allows future possibility of extension. The dedusting system with multiple suction points across the whole plant and two large filter units installed outside the building further adds to the plant’s cleanliness.”
“This “Form from Function” approach has proved effective in translating the customer’s demands into a design that fully meets their expectations: “The quality, usability and maintainability are excellent. We appreciate the appropriateness of the purpose of solutions and that the user perspective is taken into account,” comments Mauri Lielahti.
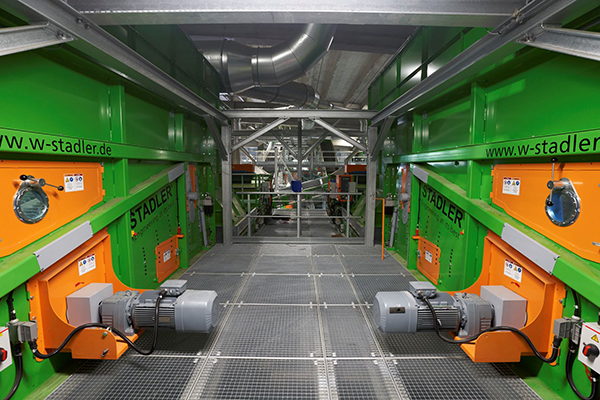
Close collaboration key to a successful outcome and completion ahead of schedule
The successful outcome of such a unique and complex project lies on the remarkable reciprocal trust and close collaboration between Remeo, STADLER and ZenRobotics – from the design phase right through to completion of the build and installation.
Nikolaus Hofmann explains: “The design phase of the project requires a lot of communication and iteration steps to find the best suitable solution. The close work between Remeo and STADLER was fantastic in defining all the specific requirements for the sorting process and the arrangement of the sorting equipment. The communication, information flow with ZenRobotics was also excellent, and enabled us to develop problem-free solutions.”
Mauri Lielahti adds: “It is no secret that the pandemic has been a challenge to us all and it has added its own challenges to our project as well. We had to do the whole planning phase in online meetings. The process has required rigorous communication, but it has worked well. STADLER’s sales team has been involved all the time and we think it is one of the cornerstones for this project being such a success. We felt that there weren’t any gaps between sales and manufacturing teams, and in our experience, this guarantees a successful project.”
The construction process was complicated by the pandemic, beginning from getting the assembly team on site, as Nikolaus Hofmann explains: “they were required to quarantine after arriving in Finland and work in bubbles, but they did a great job!” Logistics were also affected, so that “the coordination of all external suppliers and delivery of all aggregates to the site was a challenge. Some oversized transports were delayed because of problems on the ferry. We had to improvise a lot and focus all our efforts to keep to the schedule.”
In spite of these difficulties, the project was completed three and a half months ahead of schedule. “This was a great achievement, particularly in the time of the pandemic,” says Juha Mieskonen. “The assembly and installation phase of the facility ran very smoothly: day-to-day operations were well-organized throughout the process. Communication between all three parties worked very well and contributed greatly to the successful completion of the facility.”
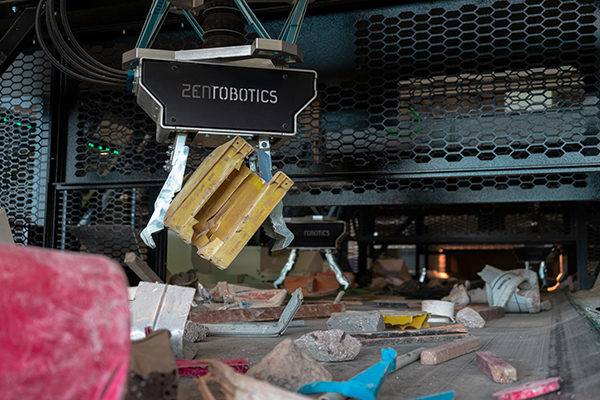
An important project on a European scale with a huge impact for Finnish waste management
Remeo’s MRF project is unique in Europe as it uses the latest technology and, thanks to its operation, material recovery will play a much greater role than energy recovery for the first time. The annual processing capacity of the facility is a 120,000 tonnes of construction waste and 60,000 tonnes of energy waste produced in commerce and industry. This waste is recycled into high-quality alternatives to virgin materials, giving the waste a new life and reducing the need for incineration.
Remeo MRF will cover more than 30 percent of all waste recycling needs in the Helsinki region in Finland. In doing so, this facility also removes the need to export the waste from Finland as the capacity to recycle waste domestically increases. Remeo’s facility offers effective recycling close to the place of origin of the waste, cutting transport emissions because of the short distances. Due to efficient recycling capabilities, Remeo is also helping its customers to meet the minimum 70 % recycling rate required by law.
The future of circular economy
Modern recycling infrastructure is crucial to enabling a speedy transition to a circular economy. The recycling industry is increasingly looking at advanced technologies to help deal with the constantly rising waste sorting requirements while increasing the top-line. Remeo’s MRF is a prime example of forerunner companies coming together to create effective and innovative solutions that pave the way for the future of waste management.