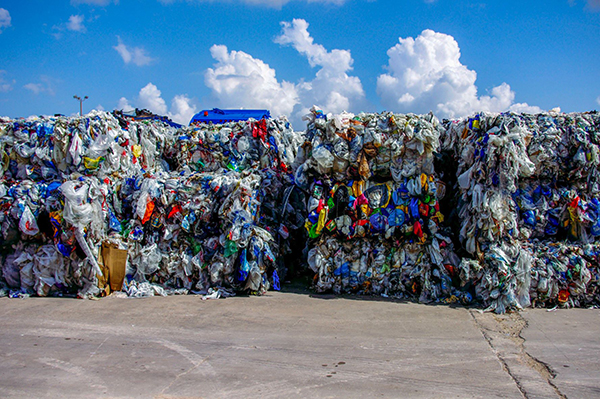
Gli imballaggi plastici flessibili e filmosi sono prodotti eccellenti dal punto di vista delle prestazioni e questo fa sì che vengano usati in modo molto esteso. Tuttavia, questi materiali presentano un problema a fine vita. Come risolverlo? Implementando un’economia circolare che li reimmetta nel ciclo produttivo. Ma il riciclo di questi prodotti richiede un approccio specifico a causa delle loro caratteristiche, un approccio che STADLER – leader negli impianti di selezione per l’industria del riciclo – applica nei suoi impianti.
La pressione ad affrontare il problema della gestione di rifiuti come gli imballaggi plastici flessibili e filmosi è aumentata, così come è cresciuta la consapevolezza sul fine vita dei rifiuti di plastica e sul loro riciclo. Oggi i consumatori sono sempre più chiari nella richiesta di un approccio più ecologico agli imballaggi. Anche la legislazione si sta rafforzando per incoraggiare i produttori a usare la resina post-consumo (PCR) oltre alla resina vergine. Per esempio, negli Stati Uniti, il New Jersey proporrà al governatore una legge che richiede il 20% di PCR nelle borse di plastica per la spesa e entro il 2025 la percentuale dovrà salire al 40%. Un disegno di legge dell’Assemblea della California rende i marchi unici responsabili del raggiungimento del 50% di PCR nei contenitori per bevande entro il 2030, con l’obiettivo di “rendere i produttori partner nel garantire materiale sufficiente per soddisfare questo requisito”. Inoltre, i grandi marchi internazionali stanno stabilendo mandati autoimposti sul contenuto di PCR nei loro imballaggi, dato che la legislazione in tutto il mondo diventerà sempre più severa.
Come risultato della pressione per la creazione di un’economia circolare della plastica, il settore del riciclo sta attirando investimenti pubblici e privati. Closed Loop Partners – una società di investimenti con sede a New York che fornisce finanziamenti azionari e progettuali per coinvolgere nell’economia circolare prodotti, servizi e infrastrutture all’avanguardia – sta partecipando all’acquisizione di una quota di maggioranza di Sims Municipal Recycling e prevede di espandere il business in altri comuni e flussi riciclabili post-consumo.
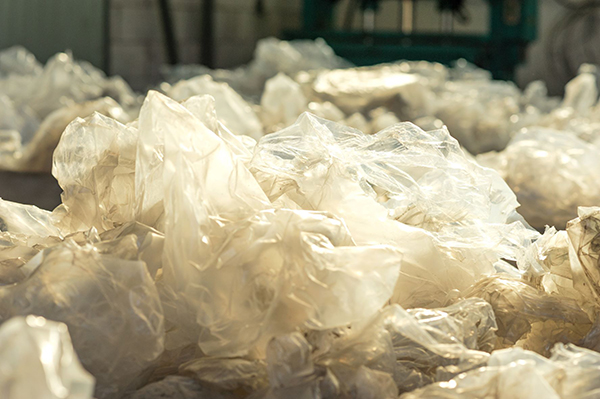
La sfida del riciclo degli imballaggi plastici flessibili e filmosi
Il riciclo degli imballaggi flessibili e filmosi presenta sfide molto specifiche e uniche. “La prima sfida è la bassa densità di questi materiali, che sono molto leggeri e vaporosi”, spiega Enrico Siewert, direttore sviluppo prodotti e mercato di STADLER. “All’interno degli impianti di selezione gli imballaggi filmosi tendono ad essere poco stabili sui nastri trasportatori e ad avvolgersi intorno ai cuscinetti degli alberi, compromettendo le prestazioni delle macchine ed incrementando la manutenzione. Inoltre, questi materiali possono intrappolare l’umidità e tendono ad accartocciarsi; di conseguenza ci vuole molta energia per pulirli”.
Tuttavia, il problema più grande è che molti di questi materiali sono multistrato e costituiti da diversi polimeri – EVOH, PE, PP o PET – sovrapposti con lo scopo di ottenere le proprietà prestazionali desiderate. Gli strati sono fusi insieme e quindi molto difficili da separare meccanicamente. Inoltre, presentano diverse temperature di fusione, quindi l’estrusione è difficile quando si utilizza questo materiale durante la produzione di nuovi prodotti.
Il riciclo meccanico non può trattare facilmente i multistrati. In alcuni casi, la soluzione può essere il riciclo chimico: “Si tratta di scomporre i polimeri plastici in olio che può essere raffinato e trasformato in combustibile o in una resina con l’obiettivo di chiudere il cerchio”, dice Enrico Siewert. Tuttavia, questo processo è ancora agli inizi, e in questa fase è molto costoso e presenta notevoli difficoltà.
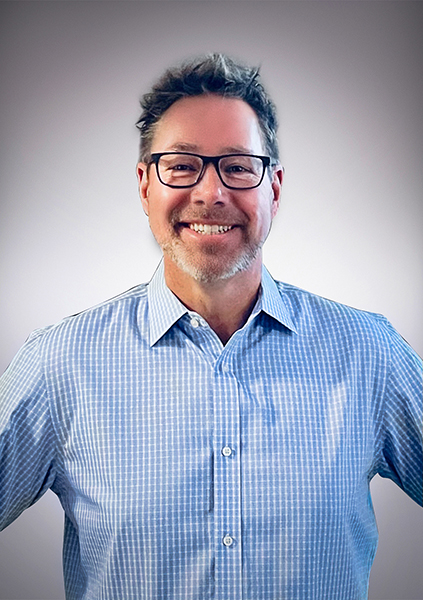
Attrezzature di selezione specifiche per un compito impegnativo
La selezione degli imballaggi plastici flessibili e filmosi richiede attrezzature specifiche come quelle di STADLER Questo per le dimensioni e il comportamento di questi materiali con determinati tipi di macchine.
Il processo inizia con i materiali – composti principalmente da PE e PP – che entrano nell’impianto di lavorazione sotto forma di balla, che viene triturata. In seguito, il materiale viene inviato ad un separatore balistico, dove viene suddiviso in due flussi, 2D e 3D. Il materiale 2D viene distribuito e passa attraverso i selezionatori ottici per isolare gli imballaggi in LDPE, PP e HDPE.
Questo è seguito dalla separazione per densità in un serbatoio d’acqua, i materiali vengono spinti verso il fondo tramite delle pale rotanti, incoraggiandone la separazione in flottanti e non. Il PE e il PP che galleggiano vengono poi macinati in pezzi più piccoli e ulteriormente puliti con acqua calda e/o fredda all’interno di macchinari dedicati. L’intero processo raggiunge un grado di separazione molto buono, con più del 70% del prodotto in uscita costituito da PE e PP (in funzione della purezza del materiale in ingresso). Il materiale viene quindi rifuso in una resina, che viene poi filtrata per rimuovere eventuali particelle di materiali estranei, come carta, sporcizia, alluminio e altri polimeri non conformi.
Il risultato di questo processo – quando non si separa il materiale all’inizio – è un pellet pulito, grigio scuro, composto da PE puro fino al 99%. Questo materiale può essere utilizzato per produrre imballaggi flessibili di plastica nera, come i sacchi della spazzatura. Può anche essere riciclato chimicamente per togliere la colorazione alla fine del processo e ottenere una resina chiara quasi vergine.
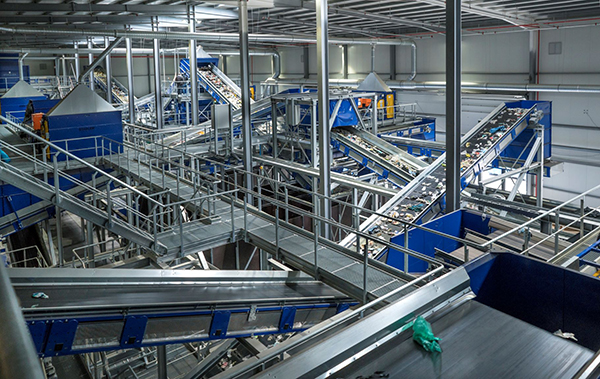
Una domanda crescente di soluzioni per la selezione di pellicole e imballaggi flessibili
Da quando ha completato il suo primo impianto per Integra, a Sofia, in Bulgaria, nel 2018, STADLER ha registrato un importante aumento della richiesta di soluzioni per la selezione di imballaggi flessibili e filmosi. I suoi separatori balistici, i Delabeler per rimuovere le etichette, e i nastri trasportatori sono il cuore della sua offerta per gli impianti di selezione delle plastiche ; ma la sua offerta si sta costantemente evolvendo in seguito all’ascolto dei clienti e allo sviluppo di nuove soluzioni ai problemi che man mano si presentano.
“Stiamo sempre sviluppando nuovi macchinari, stabilendo partnership e cercando modi per gestire questo flusso di materiale difficile da riciclare, perché i nostri clienti lo richiedono”, dice Enrico Siewert. “E stiamo perfezionando i nostri sistemi dedicati ai gestori degli impianti di riciclo chimico, che sono sempre più consapevoli della necessità di sofisticati sistemi di pretrattamento per selezionare, vagliare e lavare i materiali prima che vengano scomposti chimicamente in riciclati”.
STADLER è anche attivamente coinvolta nel dialogo in corso tra l’industria del riciclo e i grandi marchi sull’adozione di un approccio più sostenibile al packaging (“Design for Recycling”) che faciliti il recupero dei materiali a fine vita.
“In STADLER siamo bravi ad ascoltare i nostri clienti e a capire le loro esigenze. Abbiamo il team giusto e l’esperienza nel settore, siamo coinvolti nell’industria, studiamo le nuove tecnologie man mano che arrivano, in modo da consigliare i clienti sulla soluzione migliore per la loro attività, la tecnologia disponibile, e su come collocare correttamente le attrezzature per trasformare i rifiuti in prodotto finito.”