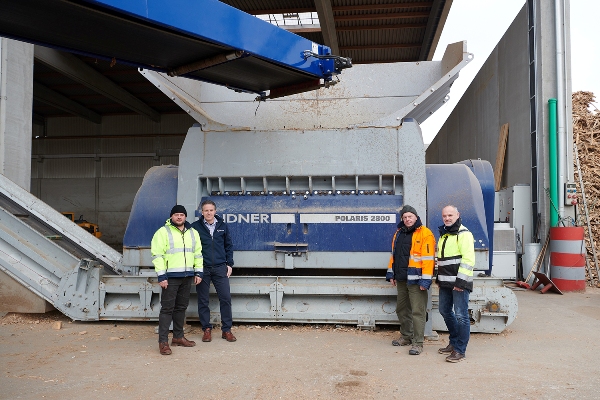
Of that Wurzer Umwelt GmbH is certain. The Wurzer Group has been relying on Lindner’s shredding technology for over ten years and has been successfully using the manufacturer’s new Polaris 2800 in waste wood processing for over a year now. The result: few fines in the output, the highest throughput with the best machine availability – consistent, reliable and safe
Wood has always played an important role in the economic life of the Upper Bavarian community of Eitting near Munich. The over one-thousand-year-old history of the town also documents the historical timber rafting and log driving on the Isar River in the early days. Today Wurzer Umwelt GmbH is part of Eittinger’s timber industry tradition. The processing of waste wood of the grades A1 to A4* is one of the backbones in the manifold business activities of waste management and recycling. “Wurzer successfully entered this segment 25 years ago,” says Hans Kenst, Signing Officer and Operations Manager who has been with the company since 1997. “We have been continuously expanding our processing capacities, including the construction of a large hall for the dry storage of A4 wood. In the last three or four years, the total quantity of waste wood processed has increased from around 30,000 to around 100,000 metric tons per year”. Kenst sees further potential for development in this dynamically growing market. Most of the material comes from demolition and restoration activities and is brought to the site by commercial C&D waste collectors.
Quality that pays
To cope with higher waste wood quantities, the processing line was updated in May 2018 with an older machine from another supplier being replaced by the Polaris 2800. Wurzer Umwelt’s experience has shown that the Lindner shredder is the ideal machine for maximum throughput with low fine particle content in the output to satisfy buyers’ quality requirements. Compared to similar single-shaft shredders on the market, the Polaris machine series has the lowest production costs per metric ton of finished material (€/t) – as proven by a study from the Austrian University of Leoben and confirmed by its users.
Made for continuous operation
Hans Kenst is also pleased with the electric drive’s energy efficiency. From an engineering perspective, the Signing Officer and Operations Manager at Wurzer Umwelt is particularly impressed by the enormous force that the Polaris exerts with its countershaft drive and, last but not least, by the shredder’s signature resistance to non-shreddables. Kenst recalls long downtimes: “The predecessor was more susceptible to foreign objects and sometimes non-shreddables in the feed caused repair work that meant it was down for two whole days”. With the Polaris from Lindner, this problem has been solved.
The roughly pre-crushed input material may still contain screws, nails, hinges and other metal parts which the upstream over-belt magnet has not picked up and removed from the material flow. The Lindner shredder is not bothered by these non-shreddables. Hans Kenst appreciates the Polaris’ ‘good behaviour’: “The safety clutch prevents machine damage even from large chunks of rock and massive metal parts which the over-belt magnet has not detected and removed. It comes to a standstill immediately, the non-shreddables are quickly removed via the hydraulic maintenance door and the machine is back up and running in no time”.
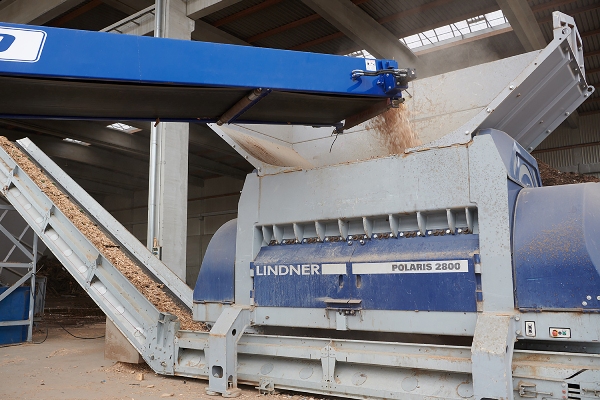
Nothing goes to waste
The fine fraction was also an issue for Wurzer Umwelt, which is why the company opted for Lindner: the Polaris 2800 shredder produces significantly fewer super fine particles than the previous solution. “Output destined for combustion with a high fines content is not readily accepted by users and you simply can’t sell it like that”, explains Hans Kenst. The Polaris’s approach of cutting the material with a relatively lower speed of 112 rpm instead of crushing it with a speed of between 800 and 1000 rpm has clearly proven to be a success.
At the facility, the waste wood is roughly pre-crushed to a size of < 300 mm and further processed in the Polaris. With a throughput of approximately 45 metric tons per hour, the machine shreds the material to an output size of < 80 mm. This way the product meets the highest quality standards and can be recovered for both energy and material use in the wood panel industry.
“Every machine is only as good as its service”
The waste wood processing facility operates nine hours a day. Hans Kenst draws a very positive balance for Wurzer Umwelt after one year of having Polaris in operation: “Lindner-Recyclingtech has been a reliable partner of ours for over ten years now. In view of the increasing quantities of processed waste wood, it was the right decision to change to Lindner in this area of the business, too. The Polaris 2800 is the ideal shredder for stationary waste wood processing. Overall, we are extremely happy with the manufacturer’s machines and services. The whole package is perfect.”
And if something goes wrong? “No worries, we have a competent contact at Lindner. The sales representative will take care of everything immediately. Things can happen, but it’s important that you get a quick response,” says Hans Kenst and states: “Every machine is only as good as its service. Which is something we really appreciate at Lindner!”
* Waste wood grades:
A1: virgin or only mechanically treated waste wood
A2: glued, colour-coated or painted waste wood
A3: waste wood with organohalogen compounds
A4: waste wood treated with wood preservatives e.g. railway sleepers, utility poles, hop poles or wine stakes (source: Wikipedia)