
L’azienda tedesca STADLER Anlagenbau GmbH, specializzata in impianti di riciclaggio e selezione, ha collaborato con la consociata weeeSwiss Technology AG per progettare e installare un avanzato impianto di selezione di rifiuti elettronici per Immark.
La nuova struttura sostituisce un impianto esistente, aumentando la capacità di lavorazione e garantendo una qualità costante e di alto livello.
Immark AG, parte del Gruppo Thommen, è un pioniere e leader di mercato nel riciclo e nello smaltimento dei rifiuti elettronici in Svizzera, con un tasso di recupero fino al 95% che supera di gran lunga i requisiti della Direttiva europea sui RAEE. L’azienda ha scelto STADLER per progettare e installare un nuovo impianto di selezione in sostituzione di quello esistente a Regensdorf, vicino a Zurigo.
“Si tratta del più grande impianto di trattamento di rifiuti elettronici della Svizzera e deve garantire un’elevata produttività e capacità di trattamento dei volumi che riceviamo”, afferma Patrick Wollenmann, Project Manager di Immark. “Con questo nuovo impianto, contiamo di aver gettato le basi per un futuro di successo in termini di gestione operativa”.
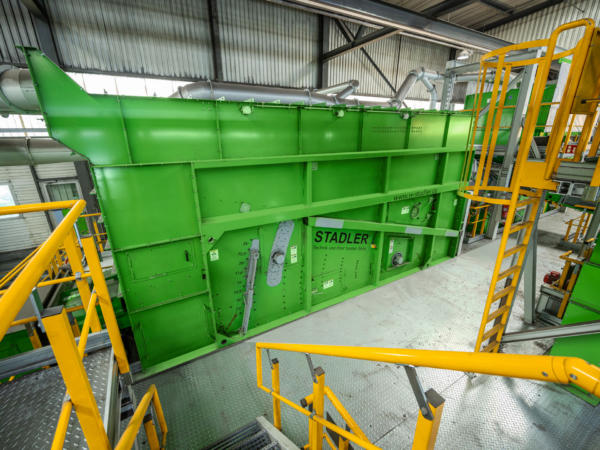
Il nuovo impianto è caratterizzato da un design innovativo e dalla tecnologia più avanzata, ed è di fatto il primo impianto di selezione di rifiuti elettronici a utilizzare un separatore balistico. L’impianto opera su due turni con una capacità di 12 tonnellate all’ora, soddisfacendo le esigenze di Immark di maggiore capacità e purezza del materiale in uscita. Inoltre, l’impianto ottimizza il recupero dei circuiti stampati.
“Per noi è stata decisiva la tecnologia dei nastri trasportatori e del separatore balistico di STADLER e la loro vicinanza a Zurigo. Apprezziamo molto anche il lavoro e la competenza dei project manager, l’implementazione rapida e costruttiva e la capacità di trovare soluzioni efficaci”, afferma Patrick Wollenmann.
“Il separatore balistico STADLER STT5000 preseleziona il materiale in tre diverse frazioni. Separa il materiale in frazione fine, plastiche piatte e cavi, oltre a materiali di forma tridimensionale come i motori elettronici”, spiega Jan Dollenmaier, coresponsabile del progetto STADLER.
Design innovativo dell’impianto per una produzione dalla qualità eccezionale
Il nuovo impianto di selezione riceve materiali appartenenti ai gruppi 1-3 (grandi e piccoli elettrodomestici e apparecchiature informatiche) e 4 (apparecchiature di consumo) della direttiva RAEE, che vengono trattati in diversi moduli di lavorazione. I moduli, che di fatto sono delle sezioni di impianto, sono posizionati in linea e sono dotati di alimentatori indipendenti per dare la possibilità di caricare il materiale in diversi punti, il che garantisce una maggiore disponibilità e flessibilità dell’intero impianto.
La struttura modulare e flessibile dell’impianto consente di regolare le macchine durante tutto il processo per garantire frazioni non ferrose, ferrose, PCB (circuiti stampati), acciaio inossidabile e plastica di qualità costante ed elevata.
Nel primo modulo del processo, il materiale in ingresso viene selezionato manualmente per rimuovere i componenti pericolosi, nonché i materiali di valore come cavi, circuiti stampati e metalli.
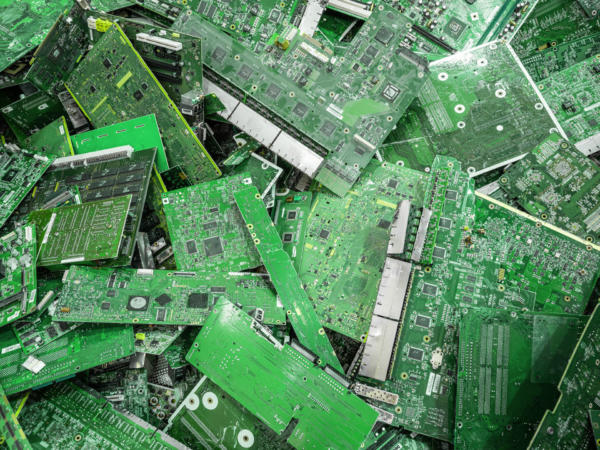
Una volta rimossi i componenti pericolosi, il materiale viene frantumato in diversi trituratori in modo da poter selezionare sia i componenti pericolosi rimanenti – come batterie o condensatori – sia i vari materiali riciclabili – come ferro, metalli non ferrosi e plastica. Nella scelta delle unità di frantumazione si è tenuto conto non solo della produzione richiesta, ma anche della minore usura possibile e della facilità di manutenzione delle macchine.
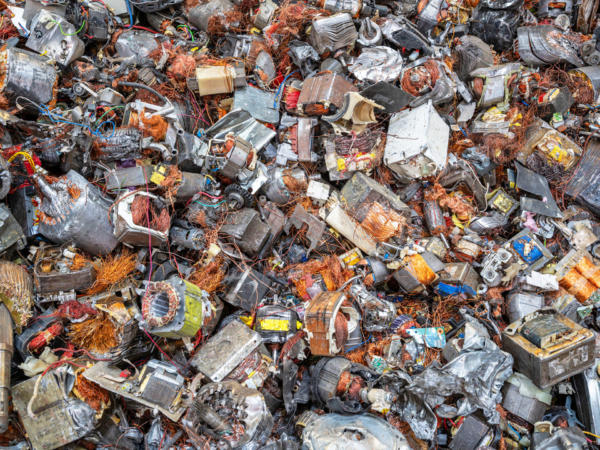
I materiali riciclabili vengono selezionati dopo la vagliatura utilizzando la più moderna tecnologia magnetica, la separazione a correnti parassite e la tecnologia di selezione a sensori. Le frazioni di ferro vengono riselezionate in una cabina apposita per garantire la qualità e aumentare il grado di purezza.
Anche la frazione fine viene sottoposta a varie fasi di selezione per separare la plastica dai composti metallici, che vengono poi macinati per separare i vari granuli metallici. Grande attenzione è stata dedicata alla protezione antincendio dell’impianto.
Dopo le unità di triturazione sono stati installati sistemi automatici di rilevamento e spegnimento degli incendi. La fonte dell’incendio rilevata viene scaricata automaticamente in un bunker d’acciaio attraverso un sistema di botole, dove il personale può spegnere il fuoco e mettere in sicurezza l’impianto.
L’elevata usura causata dal materiale trattato nel nuovo impianto ha richiesto caratteristiche di progettazione specifiche, come piastre di usura in acciaio inossidabile per rinforzare le tramogge e i nastri con protezione antincendio e antitaglio. L’impianto è stato inoltre progettato per semplificare al massimo la manutenzione. Tutti i punti chiave e i motori sono accessibili tramite piattaforme di manutenzione o scale di accesso.
Una stretta collaborazione garantisce il successo di un progetto complesso
La progettazione e l’assemblaggio del nuovo impianto hanno presentato sfide che i team di STADLER e Immark hanno risolto con successo grazie alla stretta collaborazione.
“Durante l’installazione della nuova linea il vecchio impianto doveva continuare a funzionare. Ciò significava costruire il nuovo impianto in più fasi sovrapposte al progressivo smontaggio del vecchio impianto. Inoltre, lo spazio disponibile nel cantiere era molto limitato”, spiega Patrick Wollenmann.
Il design modulare del nuovo impianto è stato un elemento chiave per il successo del progetto e per l’alta velocità di installazione: “Il design modulare delle singole unità ha limitato i tempi di assemblaggio a un periodo molto breve. Qualsiasi problema sorto durante il montaggio è stato rapidamente identificato e risolto grazie alla flessibilità dei tecnici di STADLER”, aggiunge Patrick Wollenmann. “Si tratta di un grande progetto dedicato ai rifiuti elettrici, con l’installazione di molte nuove macchine e il coinvolgimento di diversi fornitori. Avevamo molti nuovi interlocutori ma abbiamo gestito tutto alla perfezione in collaborazione con il team di Immark”, conclude Philipp Frechen, Joint Project Manager di STADLER.