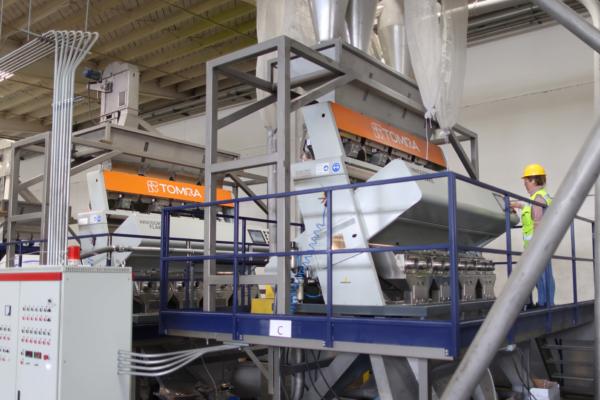
L’americana Greenpath e TOMRA utilizzano una soluzione pionieristica per la selezione meccanica delle poliolefine in base al tipo e al colore del polimero
“Lo sviluppo di un processo di selezione meccanica per chiudere il cerchio del riciclo dei tappi per uso alimentare è innovativo. La creazione di un sistema per separare in modo efficace le poliolefine miste in base al polimero e al colore con un’elevata purezza è una vera svolta”, commenta Joe Castro, presidente di Greenpath Enterprises, Colton, California.
L’azienda statunitense ha collaborato con TOMRA Recycling Sorting per installare e mettere a punto una linea di selezione di scaglie di plastica progettata specificamente per identificare e separare i tappi in poliolefina dalle bottiglie per bevande. Greenpath mira a creare per i tappi delle bottiglie lo stesso sistema di riciclo efficace che esiste per le bottiglie. “Siamo alla genesi della creazione di una selezione dei tappi simile a quella usata oggi per le bottiglie in PET”, aggiunge Eric Olsson, responsabile della divisione materie plastiche di TOMRA Recycling.
Attiva da oltre 25 anni, con sedi in California, Nevada e Texas, la Greenpath, integrata verticalmente, riceve un’ampia gamma di materiali e il flusso in ingresso può essere piuttosto diversificato. Tuttavia, è qui che Castro vede il vantaggio dell’azienda nell’offrire servizi a valore aggiunto.
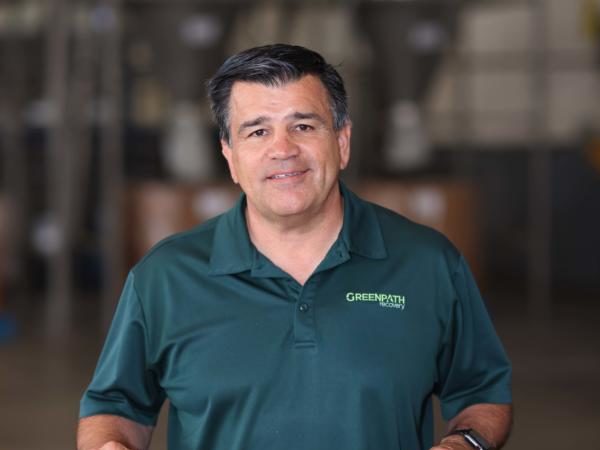
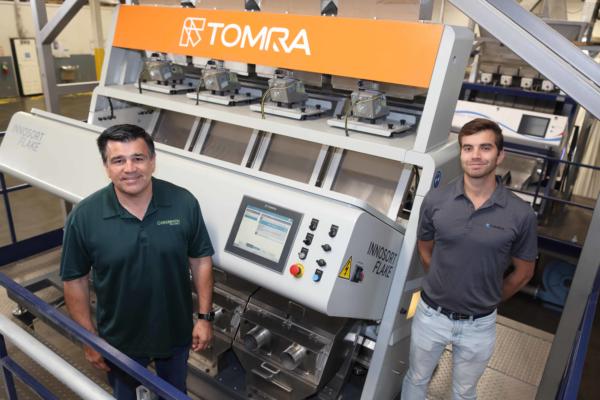
Greenpath agisce come sportello unico per fornitori e clienti, accettando carichi misti e flussi di materiale variabile e trasformandoli in prodotti uniformi e di qualità.
Tra i materiali in ingresso ci sono carta, metalli e plastica. Considerando solo il materiale poliolefinico – polietilene a bassa densità (LDPE), polietilene ad alta densità (HDPE) e polipropilene (PP) – Greenpath accetta bottiglie, pellicole, plastica rigida e, naturalmente, tappi di bottiglia. “Il polipropilene e il polietilene (PE) sono insieme la tipologia di plastica più abbondante sulla terra, ma il mercato è limitato per quanto riguarda le applicazioni di valore delle poliolefine miste riciclate”, commenta Olsson.
Purtroppo, PE e PP hanno caratteristiche di densità molto simili e sono difficili da separare nei loro diversi polimeri. Per questo motivo, le poliolefine miste vengono principalmente riciclate in applicazioni più “tolleranti” che consentono una maggiore contaminazione o una gamma più ampia di specifiche del materiale. “In alternativa, altre aziende utilizzano un approccio di ‘diluizione’ per includere le poliolefine miste, utilizzando principalmente materiale vergine e solo una piccola frazione di plastica riciclata”, spiega Castro.
Con l’obiettivo di Greenpath di fornire servizi a valore aggiunto ai propri clienti, l’enigma dei tappi in poliolefina ha tormentato Castro per 15 anni, quando l’impresa ha iniziato a lavare e trattare i tappi di bottiglia riciclati. Castro cercava un processo di selezione che permettesse di separare in modo omogeneo e di alta qualità l’HDPE dal PP, in modo da offrire ai brand e ai produttori la flessibilità necessaria per includere con fiducia la plastica riciclata nelle loro applicazioni di stampaggio a iniezione. “In definitiva, puntiamo a livelli di purezza del 98% o superiori”, spiega Castro.
La ricerca del riciclo “da tappo a tappo”
Un contenitore per bevande è comunemente composto da quattro parti: bottiglia, tappo o chiusura, anello ed etichetta. Negli Stati in cui sono in vigore leggi sul contenuto riciclato delle bottiglie, le aziende di imballaggio e di riciclo hanno fatto il primo passo, concentrandosi sulla bottiglia in PET, che costituisce la maggior parte del contenitore. Un’infrastruttura di riciclo del PET più matura ha portato i proprietari dei marchi a incorporare nelle loro bottiglie fino al 100% di materiale riciclato post-consumo.
Con l’inasprimento delle normative per aumentare la percentuale di contenuto riciclato in peso, il tappo rappresenta il prossimo componente da affrontare. “Seguendo l’approccio di Greenpath, l’industria può arrivare a una confezione con il 100% di PCR in peso utilizzando solo la selezione meccanica”, afferma Olsson.
Affinché il tappo arrivi a un impianto di riciclo come quello di Greenpath, deve farlo assieme alla bottiglia. “Altrimenti, il tappo viene eliminato nella parte anteriore del circuito e, più probabilmente, viene smaltito in discarica”, afferma Castro. Le bottiglie, le etichette, i tappi e gli anelli vengono triturati e viene utilizzato un processo di affondamento-galleggiamento per separare le bottiglie in PET dai tappi in PE e PP. Il PET più pesante affonda e le poliolefine più leggere galleggiano e vengono scremate come sottoprodotto secondario del riciclo.
La logica potrebbe suggerire di utilizzare il PET sia per la bottiglia che per il tappo per risolvere il problema, ma Olsson spiega che non è così semplice. “L’imballaggio monomateriale è un sogno a cui aspirano molti riciclatori, produttori e aziende chimiche, ma non ci siamo ancora arrivati. I diversi polimeri hanno punti di forza e di debolezza diversi”, spiega. “La filettatura del tappo, necessaria per stringere e mantenere sigillato il contenitore, è una proprietà a cui le poliolefine, PE e PP, si prestano particolarmente bene”.
Mentre alcuni riciclatori di bottiglie vedono le poliolefine miste come un materiale di scarto, Castro ci vede un’opportunità. Grazie alla sua esperienza con una varietà di materiali e alla filosofia delle soluzioni uniche per i suoi fornitori, Greenpath ha ampie capacità di lavorazione con diverse linee per la selezione di materie prime diverse. L’azienda è esperta in processi di riciclo meccanici, multimateriale e in lotti.
Per cogliere l’opportunità di chiudere il cerchio dei tappi e offrire un mercato più sostenibile per le poliolefine, Greenpath ha studiato diverse tecnologie per la selezione delle poliolefine miste. “Le densità di PE e PP sono molto vicine tra loro, quindi l’uso di vasche di galleggiamento e di affondamento non è efficace”, commenta Castro. Sono state prese in considerazione anche tecnologie di riciclo alternative, ma non hanno offerto la resa o il recupero delle resine PE e PP desiderati.
“Le rese sono basse e bisogna considerare le spese, lo spazio e i rifiuti generati dal processo di separazione”, spiega.
Greenpath ha iniziato così a puntare su una soluzione meccanica, utilizzando selezionatrici di flakes. I funzionari dell’azienda hanno iniziato a parlare con TOMRA, che aveva introdotto un nuovo tipo di tecnologia per la selezione delle scaglie. Uno dei parametri di progettazione della tecnologia era l’estrazione di valore da flussi di rifiuti plastici multicomponenti.
Olsson afferma che l’industria non ha ancora raggiunto il limite massimo per la selezione meccanica delle poliolefine. “È meglio perseguire un percorso che introduca il minor numero di modifiche al materiale e che effettui la selezione nel modo più efficiente”, afferma. “I produttori di tecnologie di selezione meccanica e chimica stanno avviando ora i primi processi per produrre i materiali derivanti dagli impegni di circolarità per il 2025 e il 2030. La produzione di flussi di polimeri con una purezza del 95% o superiore è fondamentale per molti tipi di processi di riciclo a valle e la selezione dei flakes ci può portare a questo risultato”.
Flessibilità nella selezione meccanica
Le discussioni relative agli obiettivi di Greenpath hanno portato alla scelta della selezionatrice INNOSORT™ FLAKE di TOMRA. Una caratteristica interessante per l’azienda è che la macchina non ha un grande ingombro, e si è potuta facilmente integrare nello stabilimento di Colton, in California. Dopo aver discusso la purezza, la resa e la produttività necessarie per soddisfare gli obiettivi di Greenpath, sono state installate le selezionatrici di scaglie.
Progettata per la flessibilità, INNOSORT FLAKE ha una combinazione unica di tecnologie a sensori, tra cui telecamere a colori in grado di identificare 16,8 milioni di variazioni di colore. Con telecamere su due lati, “una è posizionata su ciascun lato dello scivolo in cui cadono i materiali, in modo da poter distinguere la differenza tra un lato della scaglia e l’altro”, spiega Nick Doyle, key account manager di TOMRA Recycling. Questo aiuta a identificare l’etichettatura all’interno dello stampo che può essere un fattore di contaminazione. “Caratteristiche come queste rendono la macchina particolarmente adatta alla catena di riciclo delle poliolefine, che ha un estremo bisogno di colmare le lacune qualitative”, aggiunge.
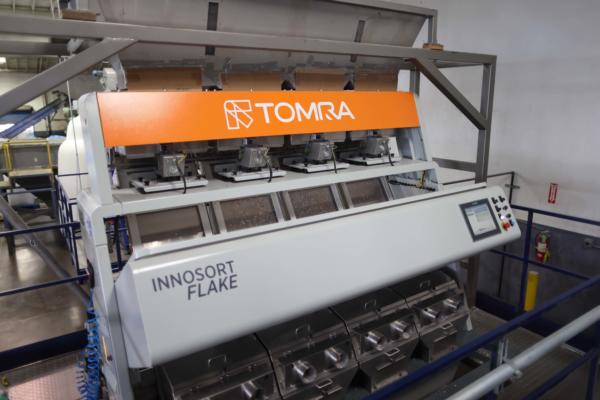
Il sistema di illuminazione FLYING BEAM offre un rilevamento rapido e affidabile dei materiali da parte dei sensori NIR (Near-Infrared). Fornendo una distribuzione omogenea della luce sull’intera larghezza del nastro (2 metri), garantisce la classificazione dei materiali PE e PP, nonché di altri polimeri e materiali. Integrata nella scatola dello scanner per proteggerlo da eventuali danni, questa tecnologia di illuminazione offre un risparmio energetico fino all’80% rispetto ai sensori di luce convenzionali.
La flessibilità della configurazione consente di effettuare – con la stessa unità – la selezione in una o più fasi. “Possiamo affidare alla macchina più attività di selezione per scivolo e persino dividere uno scivolo in due o più flussi di processo diversi”, spiega Doyle.
“Possiamo effettuare più passaggi attraverso una macchina o collegare più macchine in serie per ottenere i risultati desiderati”.
Castro ammette che la varietà delle materie prime ricevute da Greenpath pone problemi di selezione, ma l’azienda è riuscita a superare questo problema grazie ad anni di esperienza fornendo un prodotto riciclato di alta qualità. Tuttavia, l’azienda si è ritrovata con un materiale poliolefinico misto. “La tecnologia di TOMRA ci permette di portare il materiale riciclato a un altro livello, purificandolo a un livello superiore e questo apre l’opportunità di riciclo circolare ‘da tappo a tappo’”, afferma.
Materiale più uniforme
Ciò che rende Greenpath un vantaggio per i suoi fornitori lo rende anche un ostacolo per la selezione dei flakes di poliolefine. La variabilità del materiale in ingresso, oltre al fatto che questa è la prima struttura in Nord America a tentare questo tipo di selezione di poliolefine miste, ha richiesto un’attenzione particolare ai dettagli per ottimizzare la selezione. “Queste macchine sono di per sé ottimali in un flusso a regime”, spiega Olsson, “e devono quindi lavorare insieme come un sistema di processo olistico, insieme ad altri tipi di apparecchiature”.
Le due aziende si sono impegnate per ottenere il processo giusto. “Prima di scegliere TOMRA abbiamo cercato un’azienda che ci supportasse in questo percorso. Un produttore avrebbe potuto semplicemente dire: ‘Conoscete l’attrezzatura e le sue funzioni, quindi andate a scoprirvele da soli'”, dice Castro. “Tuttavia, TOMRA è stata di grande supporto in questo progetto, ed è stata più che altro un partner, in grado di comprendere che sarebbe stato necessario un ulteriore supporto per trovare il processo giusto”.
Per raggiungere gli obiettivi di elevata purezza di PE e PP monopolimero di Greenpath da materie prime poliolefiniche miste, entrambe le parti hanno analizzato l’intero processo di selezione. Anche se c’è ancora un po’ di lavoro da fare nell’impianto di Colton, “la fattibilità meccanica c’è”, conferma Olsson.
“Il sistema è ora in grado, tramite le unità INNOSORT FLAKE, di effettuare la selezione dei prodotti in PE o PP per polimero e poi per colore – come il rosso, il bianco, il blu, l’arancione o il verde; possiamo purificarli e fornire loro un colore selezionato che soddisfi la loro specifica applicazione utilizzando la la plastica riciclata post-consumo”, afferma Castro.
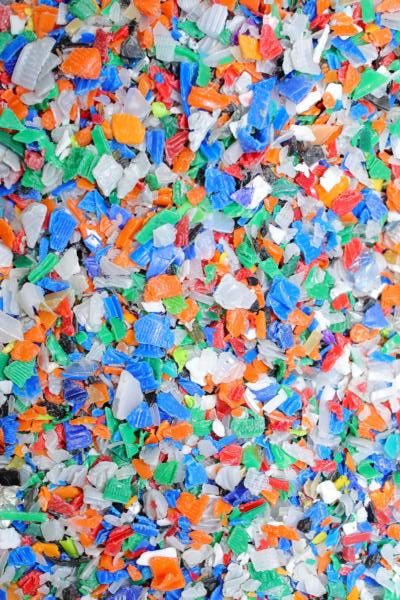
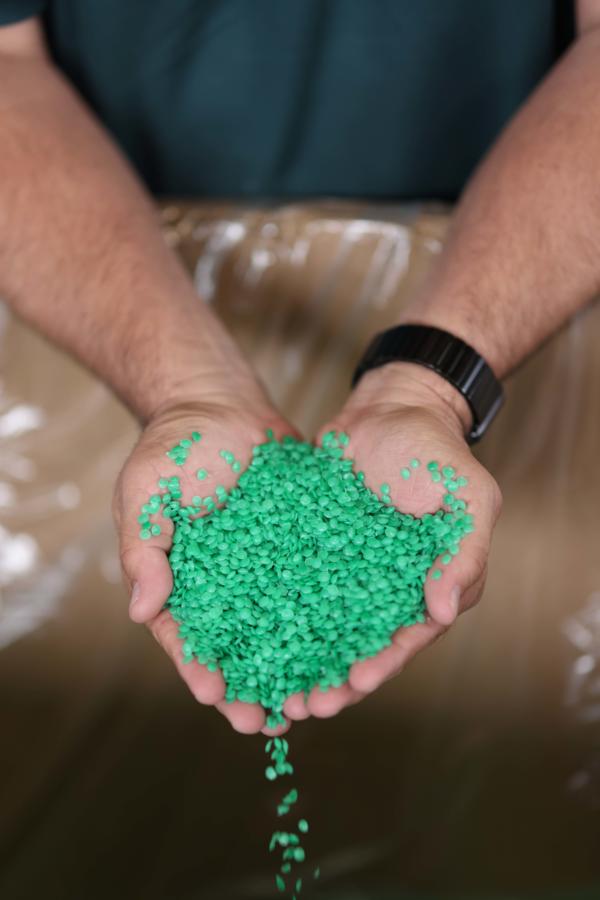
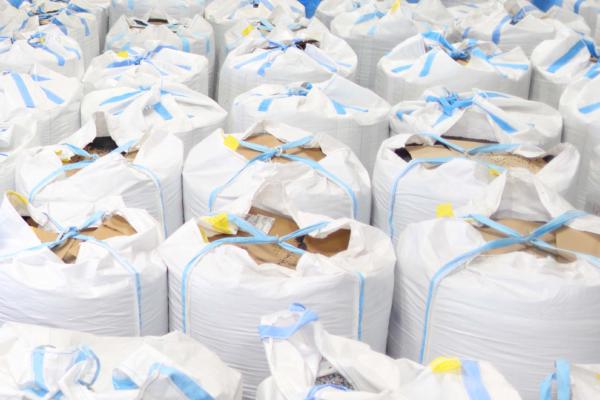
Olsson di TOMRA mostra ottimismo per quanto è stato realizzato con Greenpath, per il suo impatto sul mercato delle poliolefine miste e per il significato che ha per le aziende di imballaggio che cercano di raggiungere gli obiettivi di contenuto riciclato. “Stiamo iniziando solo ora a sfruttare questa opportunità”, dice. “Siamo all’inizio del ciclo chiuso dei flussi di rifiuti misti di poliolefine. Non sarà più solo un sogno irrealizzabile!”
TOMRA Recycling
TOMRA Recycling progetta e produce tecnologie di selezione basate su sensori per il settore globale del riciclo e della gestione dei rifiuti, per trasformare il recupero delle risorse e creare valore.
L’azienda è stata la prima a sviluppare applicazioni avanzate di selezione di rifiuti e metalli e ad usare la tecnologia a infrarossi NIR per estrarre frazioni preziose dalle risorse, mantenendo il materiale in un ciclo di uso e riutilizzo. Ad oggi, 9.000 impianti sono stati installati in 100 Paesi.
TOMRA Recycling è una divisione del gruppo TOMRA, fondato nel 1972 grazie a un’innovazione che iniziò con la progettazione, fabbricazione e vendita di macchine per la raccolta automatica dei contenitori usati delle bevande (reverse vending machines).
Oggi, TOMRA guida la rivoluzione delle risorse per trasformare il modo in cui queste vengono ottenute, usate e riutilizzate per un mondo senza rifiuti. Le altre divisioni del gruppo sono TOMRA Food, TOMRA Mining e TOMRA Collection.
TOMRA ha circa 105.000 installazioni in oltre 100 mercati e nel 2022 ha dichiarato un fatturato di 12 miliardi di NOK. Il Gruppo, la cui sede è ad Asker (Norvegia), dà lavoro a 5.000 persone ed è quotato sulla Borsa di Oslo (Oslo Stock Exchange).
Per maggiori informazioni su TOMRA, visitate il sito www.tomra.com e seguite TOMRA Recycling su Facebook, Twitter e LinkedIn.