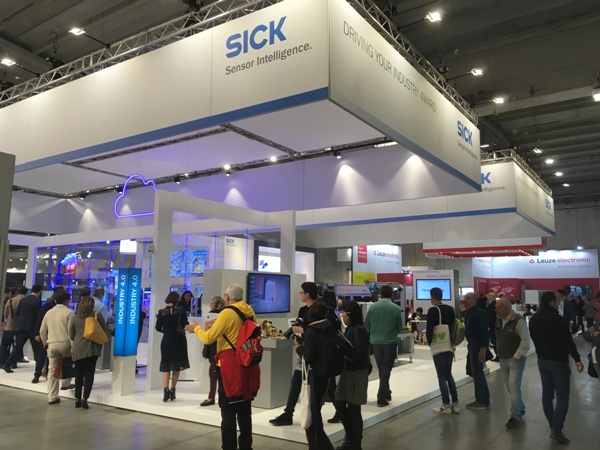
Un aumento del fatturato e dei dipendenti del Gruppo SICK, ma non solo: anche i sensori continuano a crescere in termini di funzionalità e intelligenza
SICK ha chiuso l’anno fiscale 2018 con successo: +10,3% di ordini, +8,3% di fatturato, +10,5% di assunzioni. “Il fatturato ha ormai superato 1,6 miliardi di euro e il nostro organico sfiora i 10.000 collaboratori. Stiamo crescendo velocemente, su ogni fronte”. Così Costantino Ghigliotti, uno dei Managing Director di SICK S.p.A., ha aperto la conferenza stampa a SPS Italia a Parma.
“I valori di EBIT sono scesi di quasi 2 punti percentuale”, ha proseguito Ghigliotti, “ma questo dato non ci spaventa perché deriva dai nostri investimenti in R&D. La creazione di nuove start-up interne, ad esempio, e lo studio sempre maggiore su Digitalizzazione e Deep Learning richiedono molte energie. Le novità che vedrete oggi derivano proprio dalle nostre attività di ricerca, ma non vogliamo fermarci qui. Abbiamo bisogno di continuare a studiare nuove soluzioni per il futuro”.
Sicurezza al primo posto
La conferenza stampa di SICK si è aperta nel District 4.0 di SPS, davanti a un cobot che sfida i visitatori nel gioco dei dadi. “Questa demo sembra molto semplice, eppure non lo è affatto”, ha esordito Luigi D’Alessio,LifeTime Services Manager Factory Automation. “Sviluppata interamente da SICK, l’applicazione sfrutta tutte le potenzialità della nostra sensoristica: sistemi di visione, un nuovissimo sensore per la calibrazione del robot, laser scanner e centralina di sicurezza programmabili, dispositivi di lettura/scrittura RFID e molto altro. Solo grazie a questi strumenti l’applicazione diventa collaborativa”.
I cobot portati a SPS hanno dimostrato proprio la complessità di questi sensori. Tra tutte le soluzioni implementate, è emersa subito una grande novità: WFZ. Studiato appositamente per le applicazioni di robotica che richiedono massima precisione, questo dispositivo permette la calibrazione del Tool Center Point. Con un pulsate si attiva una specifica funzione del robot che aiuta il braccio a riposizionarsi precisamente nello zero point e ricentrarsi rispetto agli assi x, y e z.
Nonostante lo scopo prettamente ludico delle demo presentate, grande attenzione è stata posta all’aspetto della sicurezza: “I cobot devono prestare molta attenzione a quello che accade nello spazio che li circonda per potersi muovere senza costituire un pericolo per l’operatore”, ha proseguito D’Alessio.
Oltre ad essere leader nella produzione della sensoristica, SICK offre anche un fondamentale servizio di consulenza denominato Safety Service, che supporta il cliente dalla valutazione dei rischi all’identificazione delle soluzioni più efficienti ed efficaci per innalzare i livelli di sicurezza di macchine e impianti. Safety Service è, a tutti gli effetti, un pacchetto chiavi in mano perché comprende anche la fornitura e l’installazione dell’hardware, oltre alla validazione delle installazioni secondo le norme di riferimento, al supporto e al training sia sui prodotti di sicurezza che su direttive e norme vigenti.
Laser scanner di sicurezza da record
“A proposito di sicurezza, il 2019 rappresenta l’anno dei primati per i nostri laser scanner”, ha affermato Alberto Biraghi, Market Application Engineer Industrial Safety, “A SPS stiamo presentando tre prodotti di punta pronti a dettare nuovi standard: il primo laser scanner di sicurezza al mondo certificato per l’uso outdoor, il laser scanner più piccolo del mercato e anche quello con campo di lavoro più ampio”.
Tutti e tre i modelli proposti si basano sul tempo di volo per il monitoraggio delle aree di protezione. Una delle esigenze più sentite dal mercato riguarda la possibilità di utilizzare in sicurezza AGC e AGV anche al di fuori delle aree produttive, ma per molto tempo ciò è stato impossibile: i laser scanner di sicurezza indoor, infatti, non hanno le certificazioni idonee per lavorare in esterno e di conseguenza non ne garantiscono il corretto funzionamento all’aperto. Oggi questo limite è stato superato: con outdoorScan3 per la prima volta i sistemi a guida automatica possono muoversi in sicurezza anche all’esterno. Grazie alla tecnologia safeHDDM® il sensore opera senza alcuna difficoltà con elevata intensità luminosa, ed è capace di filtrare i disturbi legati alla caduta di pioggia e neve oltre che di lavorare in presenza di nebbia.
OutdoorScan3 stupisce anche per le sue ottime performance: l’apertura ottica è di 275° e la portata dell’area di sicurezza è di 4 m, mentre l’area di warning può arrivare fino a 40 m. Inoltre, nella versione Pro – EtherNet/IPTM è possibile programmare fino a 128 campi di protezione, di cui 8 possono agire in contemporanea. Per applicazioni più semplici, outdoorScan3 è disponibile in versione I/O.
NanoScan3 e microScan3 Core, invece, sono entrambe soluzioni che funzionano in ambienti indoor. Le dimensioni di appena 101x101x80mm rendono nanoScan3 il più piccolo laser scanner di sicurezza del mercato. Grazie all’housing compatto ma dalle potenti funzionalità è adatto, ad esempio, ad applicazioni di robotica collaborativa.
Il primato segnato da microScan3 Core, invece, riguarda il l’area di sicurezza, che si estende fino a 9 m. Risulta, quindi, adatto nelle macchine utensili, nelle isole robotizzate e nelle grandi linee di produzione dove solitamente vengono impiegati più dispositivi di sicurezza.
Motori più prestanti per impianti più intelligenti
Quando si parla di motorfeeback si parla di HIPERFACE DSL®, il protocollo sviluppato dal team ingegneristico della filiale torinese di SICK che ha rivoluzionato il mondo dei servodrive.
“Da decenni SICK si occupa di sensori per feedback motori che forniscono dati legati alla posizione”, ha evidenziato Roberto Pollini, Head of Industrial Automation Solutions Unit. “Dati che, da soli, non sono più sufficienti per soddisfare le richieste dell’Industry 4.0. Per questo motivo, già dal 2011, proponiamo una tecnologia a cavo singolo capace di fare molto di più”.
La nuova linea di Smart Motor Sensors nasce, quindi, per aiutare costruttori di macchine e impianti nell’offrire soluzioni sempre più avanzate, ed è composta da motorfeedback che sfruttano HIPERFACE DSL® per il controllo in real time non solo dei motori, ma dell’intero impianto. I dati raccolti, infatti, riguardano posizione, temperatura nel motore e nell’area circostante, velocità, vibrazioni, costanza della tensione e cicli. Le informazioni vengono visualizzate tramite istogrammi generati ogni minuto, per monitorare lo stato del sistema e anche per scopi di manutenzione predittiva. Il tutto, lo ricordiamo, con un solo cavo.
L’ultimo nato nella famiglia degli Smart Motor Sensors è EDx35, un sistema motorfeedback digitale disponibile sia in versione SingleTurn che MultiTurn per motori sincro di taglia 40. La serie stupisce per numerose caratteristiche: la risoluzione di 24 bit per il singolo giro, l’assenza di batteria tampone che si traduce in assenza di manutenzione per usura, la trasmissione di posizione assoluta – velocità – accelerazione ogni 12µs. Inoltre, lo storage avviene automaticamente nella EEprom ogni 20 minuti con istogrammi di controllo. Il sensore, molto compatto, può essere installato ovunque e, grazie alle diverse taglie in cui è disponibile, può essere utilizzato anche in applicazioni stand alone.
EDx35 sfrutta il protocollo HIPERFACE DSL®, quindi garantisce un cablaggio semplice e veloce: per la messa in servizio bastano due cavi inseriti nell’unico connettore di potenza montato nel motore. Senza dimenticare che HIPERFACE DSL® è già pronto per i livelli Safety SIL2 e SIL3 per quanto riguarda la posizione.
Le fotocellule del futuro: personalizzabili, flessibili e dal feedback immediato
Il concetto di “one cable” per la trasmissione dei dati e il collegamento dei sensori ritorna anche nelle fotocellule con FlexChain, un innovativo concetto di connettività che risulta particolarmente interessante per il mondo della logistica, ma che può essere adottato in svariati altri settori. FlexChain riguarda la possibilità di collegare fino a 60 sensori fotoelettrici in cascata con un unico cavo I/O lungo 40 m. E ancora: SICK offre la possibilità di mixare tra loro fotocellule catarifrangenti, a tasteggio o a emettitore/ricevitore, senza alcun rischio di interferenza dal momento che la catena è gestita con la stessa logica delle barriere, quindi con l’interrogazione di una sola ottica alla volta. “Il vantaggio è subito evidente: creare una barriera fotoelettrica personalizzata al 100%”, ha dichiarato Mauro Casellato, Product Manager Photoelectric Sensors. “In più il commissioning avviene con un unico pulsante, evitando di nominare sensore per sensore al PLC, mentre l’host che gestisce la comunicazione ha il controllo totale di quello che accade ad ogni singolo dispositivo”.
In caso di ottica sporca, guasto o problemi di apprendimento, infatti, viene subito inviato un segnale di allarme che indica su quale sensore è stato rilevato il problema. I dati registrati vengono rielaborati e trasformati da un gateway in IO-Link, CANopen o RS485 e si sta valutando anche una versione con uscita in PROFINET ed EtherCAT.
Un’altra importante novità è data da RAY26 e RAY10, due nuove varianti di Reflex Array, ossia fotocellule che utilizzano fasci di luce laminare al posto della luce puntiforme per rilevare con affidabilità oggetti trasparenti, irregolari, perforati e di altezze diverse.
Caratteristica unica nel mercato di RAY26 è l’altezza del fascio di luce che arriva fino a 55 mm con una portata massima di 4,5 m. Grazie all’ottica autocollimata, inoltre, il catarifrangente può essere posto a distanze molto ravvicinate, andando ad eliminare le zone cieche.
RAY10, invece, si differenzia per le sue dimensioni compatte di soli 21,5x36x37,3 mm che gli consentono, comunque, grandi performance: fascio di luce di 25 mm, portata massima di 1,5 m e zona cieca di 0,5 m per rilevare oggetti a partire da 5 mm.
SICK si è spinta ancora oltre, dotando queste fotocellule di IO-Link di serie, fondamentale per impostare aree di blanking. In questo modo si possono, ad esempio, oscurare i bordi esterni dei conveyor, soggetti a frequente usura e, quindi, pericolosi per la generazione di falsi rilevamenti.
Sempre grazie ad IO-Link viene fornito un doppio segnale di allarme in caso di contaminazione dell’ottica e/o del riflettore: uno visivo, come la maggior parte delle fotocellule del mercato, e uno, appunto, tramite IO-Link.
Sensori collegati in rete nel banco prova 4.0 di SICK
“Non solo la fabbrica del futuro, ma già quella del presente è orientata verso la mass customization”, ha proseguito Marco Catizone, Head of Industrial Integration Space. “Elementi chiave devono essere la connessione e la digitalizzazione dei processi: solo così la produzione può adattarsi in modo flessibile e rapido alle richieste di personalizzazione del prodotto, sempre più frequenti”.
Per essere pronta a superare questa sfida, SICK si è messa in gioco, costruendo un nuovo centro produttivo a Hochdorf, in Germania. Il nuovo stabilimento è stato progettato seguendo tutti i dettami di Industry 4.0 e funziona come una sorta di banco prova delle soluzioni SICK. Nei 1.050 mq di Smart Factory vengono realizzate 5 famiglie di fotocellule di ultima generazione, declinate in 500.000 varianti. “Con un così alto numero di versioni è importante che tutto funzioni alla perfezione e che la produzione venga riorganizzata in tempo zero per poter evadere l’ordine in una breve finestra temporale e garantire una produzione massima di 1,2 milioni di pezzi all’anno”, ha specificato Catizone.
La Smart Factory si compone di 12 moduli di assemblaggio automatici, indipendenti fra loro, e 4 stazioni manuali. La produzione viene organizzata in tempo reale fra i vari moduli, attraverso un software di gestione realizzato direttamente da SICK. Il flusso dei materiali avviene tramite veicoli autonomi (AGC).
La demo presentata in fiera ha mostrato da vicino come è fatta una fabbrica 4.0: AGC e cobot lavorano al fianco degli operatori in totale sicurezza, mentre una dashboard trasforma tutte le operazioni svolte in formato digitale. L’efficienza della fabbrica è messa nero su bianco, con indicatori di produzione per i manager dell’impianto, ma anche con la possibilità di analizzare i dati di ogni singolo sensore installato per verificarne il corretto funzionamento e realizzare una manutenzione predittiva.
Ma come è possibile avere tutti questi dati? La risposta arriva da Pasquale Cara, Product Manager Electromagnetic Sensors and Industrial Instrumentation: “SICK ha sviluppato FieldEcho®, un software che consente di mappare, controllare e monitorare una rete di sensori, indipendentemente dalla loro marca. Unica condizione necessaria è che siano dotati di IO-Link”.
Grazie al protocollo di comunicazione IO-Link, infatti, anche i semplici sensori click-clack possono scambiare informazioni sia in uscita, per la diagnostica, che in ingresso, ad esempio un dato di parametrizzazione per il cambio formato. Attraverso IO-Link è possibile individuare i malfunzionamenti e intervenire tempestivamente, senza causare fermi impianto, per un aumento della produttività.
FieldEcho®, che gira su PC e si connette alla macchina tramite il PLC in uso, permette anche di comunicare con applicazioni di livello superiore, come ad esempio applicazioni Cloud. Questo fornisce vantaggi in termini di risparmio di tempo in fase di commissioning e consente la generazione di dashboard attraverso cui tenere sotto controllo lo stato di ogni singolo sensore della macchina. Inoltre, è possibile impostare delle soglie di allarme per evidenziare eventuali anomalie e sistemarle in breve tempo.