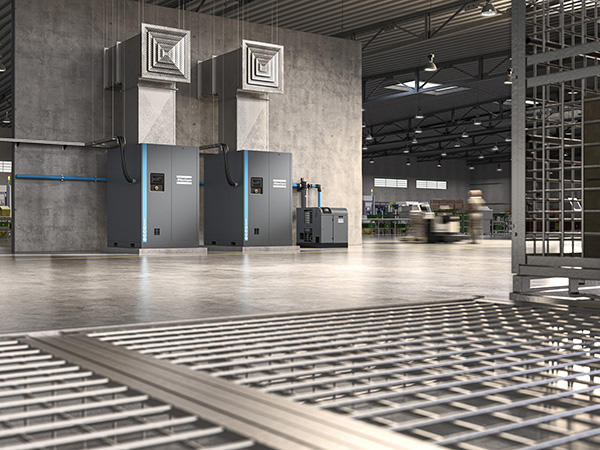
La riduzione dei consumi energetici dei nuovi compressori d’aria a velocità fissa confermano l’impegno di Atlas Copco verso una società a basse emissioni di carbonio
La tecnologia dei nuovi compressori di Atlas Copco è la dimostrazione dell’impegno dell’azienda nello sviluppo di prodotti che favoriscono la decarbonizzazione migliorando la sostenibilità ambientale delle aziende che li utilizzano. Dall’analisi dell’impronta di carbonio del Gruppo, infatti, è emerso che la maggior parte delle emissioni CO2 del Gruppo sono legate alla “fase utente”, cioè all’utilizzo da parte delle imprese dei prodotti sviluppati dall’azienda.
Parliamo dei compressori d’aria rotativi a vite a velocità fissa di nuova generazione, con un aumento della portata d’aria fino al 4% e un’efficienza energetica fino al 3%, rispetto alle macchine della gamma precedente. Si tratta dei nuovi compressori raffreddati ad olio, i GA 55 e GA 75, e la loro versione “intelligente”, i GA⁺, utilizzati ad esempio nelle industrie del packaging, della meccanica, dell’elettronica e nei cementifici. Sono compressori a velocità fissa, la cui caratteristica principale è il fatto di non potere regolare il flusso di aria in uscita, che quindi è al massimo, oppure completamente nullo. Sono utilizzati in ambiente industriale per applicazioni che richiedono una portata d’aria costante, oppure in grandi impianti di aria compressa per raggiungere in modo efficiente portate rilevanti, oltre le quali le variazioni del flusso richieste sono soddisfatte dai compressori a velocità variabile, macchine più sofisticate, ma anche più costose. I nuovi modelli GA e GA⁺ sono fra i primi compressori a velocità fissa in grado di raggiungere risparmi energetici significativi.
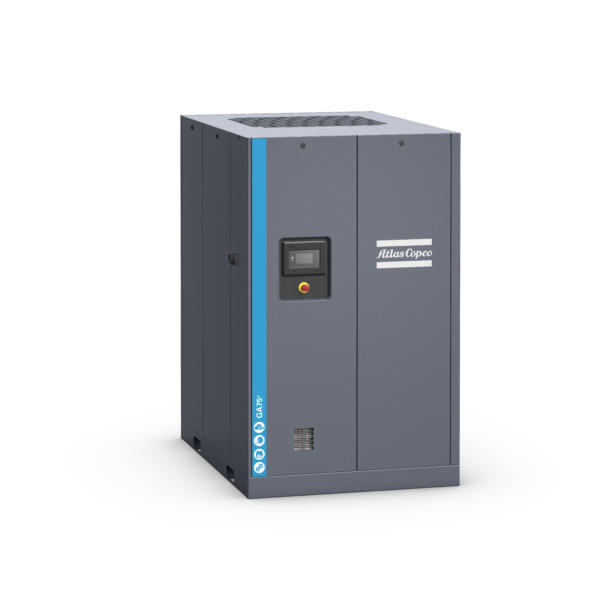
I risultati ottenuti da un test sul campo, confrontando in condizioni reali di funzionamento i nuovi compressori con il nuovo GA 75 e GA 75⁺ con il modello di pari potenza della gamma precedente, hanno avuto come risultato un risparmio energetico annuale rispettivamente di circa 6.800 euro e 16 tonnellate di CO2, e di circa 16.000 Euro e 36 tonnellate di CO2. I test sono stati fatti, a parità di condizioni di funzionamento, di installazione e di richiesta di aria da parte delle utenze, misurando l’energia consumata dalle tre macchine in una settimana di funzionamento a tempo pieno (24 h / 7gg), quindi moltiplicando questi dati per 48 settimane lavorative in un anno.
La riduzione dei consumi è dovuta, oltre al motore con classe di efficienza IE4, al nuovo modulo elettronico, presente sui modelli GA⁺, in grado di ridurre fino al 15% il tempo di funzionamento della macchina “a vuoto” riducendo proporzionalmente i consumi energetici. Ulteriori elementi innovativi sono i cuscinetti a sfera ibridi in materiale ceramico, grazie ai quali il gruppo stadio-motore ha una vita media utile superiore di circa il 33% rispetto alla macchine della generazione precedente, il sovradimensionamento dei sistemi di raffreddamento, e un sofisticato sistema di sensoristica che permette, grazie al sistema di controllo Elektronikon® Touch e al monitoraggio continuo tramite SMARTLINK il monitoraggio remoto della macchina e l’ottimizzazione dell’intero sistema. L’insieme di queste caratteristiche allungano gli intervalli di tempo di manutenzione che raggiungono le 4.000 ore per i modelli GA e le 8.000 ore per i modelli GA⁺. Da non dimenticare, inoltre, che anche questi compressori sono dotati del protocollo di comunicazione OPC UA, fra i più affermati standard nel settore dell’automazione industriale, grazie a cui il sistema di gestione dell’aria compressa può essere integrato con l’intero sistema di produzione aziendale.
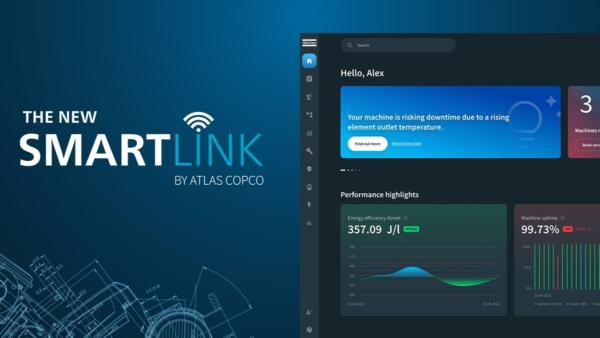
“I test effettuati hanno dimostrato che il sistema automatico di riduzione del funzionamento a vuoto ha un ruolo determinante ai fini della riduzione della spesa energetica e quindi dei tempi di recupero dell’investimento, che in casi specifici possono essere inferiori ai 18 mesi. A breve saranno installate anche in Italia le prime macchine, che confermeranno i risultati ottenuti dalle simulazioni”, afferma Paolo Montrasio, Product Marketing Manager di Atlas Copco.