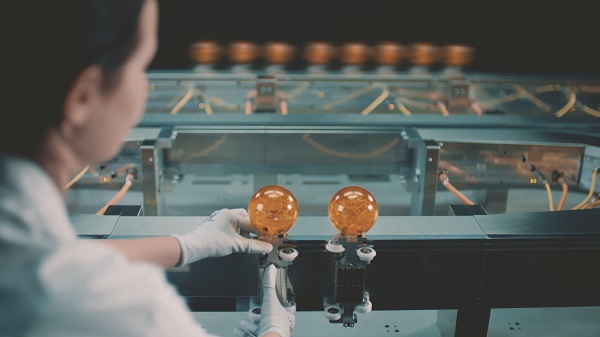
Digitalizzazione in pista
La digitalizzazione da sola non è sufficiente a ottenere una vera personalizzazione di massa e una produzione batch-of-one. queste pietre miliari IIoT si baseranno in ugual misura su nuovi approcci alla progettazione meccanica e all’hardware di controllo del movimento. Innovaziopni rivoluzionarie in queste due aree costituiscono il cuore di ACOPOStrak – un sistema di trasporto intelligente il cui design rivoluzionario consente sistemi di produzione adattivi e promette una nuova era nella produzione flessibile ed efficiente.
Le aziende manifatturiere sono costantemente alla ricerca di soluzioni che consentano di introdurre nuovi prodotti sul mercato e renderli più competitivi sul mercato a livello globale. Il punto cruciale della sfida è trovare un modo per massimizzare l’efficienza complessiva delle apparecchiature (OEE) e la produttività, anche quando si producono prodotti personalizzati in lotti di uno. “Il tema molto discusso della digitalizzazione basato su tecnologie e software di comunicazione richiede un focus troppo ristretto” sostiene Robert Kickinger, manager di tecnologie meccatroniche presso B&R. Una nuova generazione di requisiti richiede anche una riflessione radicale sul nuovo modo in cui i prodotti vengono trasportati attraverso le macchine e i sistemi di produzione – e B&R ha accettato la sfida: “Nello sviluppo del sistema di trasporto intellogente ACOPOStrak”, dice, “abbiamo impostato la base per concetti rivoluzionari di macchine nuove”
Il deviatore massimizza l’OEE
Quindi, cos’è che rende il sistema di trasporto intelligente così unico per l’automazione dei processi adattivi? “Il deviatore è – letteralmente – un componente fondamentale del sistema”, spiega Kickinger. “È al 100% elettromagnetico e quindi completamente privo di usura.” Come un incrocio autostradale, il deviatore ACOPOStrak consente ai flussi di prodotto di divergere e convergere. “Il deviatore consente alle navette di cambiare traccia a piena velocità senza compromessi in termini di produttività”, sottolinea.
Gli articoli prodotti in serie, come le bevande in bottiglia, possono essere raggruppati al volo in confezioni da sei confezioni personalizzate – tre di un sapore, due di un altro e un terzo – senza modifiche all’hardware. Il deviatore consente inoltre di risolvere i prodotti difettosi non appena vengono identificati, anziché continuare fino alla fine della linea come farebbero in un sistema convenzionale. Ciò ha un effetto positivo sulla produttività generale.
Elaborazione parallela
ACOPOStrak e i suoi divertitori aggiungono anche una nuova dimensione di flessibilità per l’implementazione dell’elaborazione parallela. Il flusso del prodotto può essere diviso, passare attraverso più stazioni di elaborazione e quindi convergere ulteriormente lungo la linea. In questo modo, la velocità di produzione non viene più limitata dalla stazione con il tempo di elaborazione più lento. “Il cliente finale può aumentare la produttività senza un corrispondente aumento dell’impronta della macchina”, spiega Kickinger ex-plains. In altre parole, ACOPOStrak aumenta l’output per metro quadrato. “In definitiva, ciò significa un ROI più elevato”, aggiunge. Quando si costruisce una macchina o una linea utilizzando questo sistema di trasporto intelligente, si ha la modularità e la flessibilità per aggiungere singoli segmenti di traccia e stazioni di elaborazione in risposta alle variazioni della domanda. Le macchine veramente adattive e scalabili immaginate per l’IoT industriale diventano realtà.
Anche i sistemi di produzione basati su ACOPOStrak sono eccezionalmente tolleranti ai guasti. Se c’è un problema con una valvola in una linea di imbottigliamento, le bottiglie semplicemente non vengono più inviate a quella valvola. La valvola difettosa non produce rifiuti, il che fa una grande differenza nel fattore di qualità OEE.
Passaggio a zero interruzioni di servizio
Le navette hot-swappable possono essere sostituite senza attrezzi e al volo per una disponibilità senza precedenti. Quando si cambia prodotto, tutto ciò che l’operatore deve fare è posizionare le ruote della nuova navetta sulle guide. I rubinetti sono tenuti in pista esclusivamente da magneti permanenti. Il cambio e il servizio possono essere resi ancora più efficienti includendo una corsia dei box nel tracciato. “Un modo di pensare è come la panchina dell’hockey su ghiaccio”, afferma Kickinger. Le nuove navette vengono montate nella corsia dei box e quindi convogliate verso le linee di produzione attuali della pista tramite un deviatore. Allo stesso modo, qualsiasi navetta non più necessaria può essere semplicemente reindirizzata sulla corsia dei box. “Tutto ciò avviene a piena velocità di produzione”, sottolinea Kickinger.
L’assoluta flessibilità di progettazione di ACOPOStrack consente di trasformarsi in tutti i tipi di layout aperti e chiusi organizzando i segmenti in diverse combinazioni su una griglia. Il nucleo del sistema di binari è un motore lineare assemblato da quattro tipi di segmenti modulari: un segmento rettilineo, un segmento di 45 ° e due segmenti di 22,5 °: uno curvo a destra, l’altro a sinistra. “ACOPOStrak si adatta perfettamente a qualsiasi sito di produzione”, spiega Kickinger. “E allo stesso tempo, apre macchine completamente nuove che non sono mai state possibili prima”.
Altamente dinamico e flessibile
Il sistema di trasporto intelligente offre molto più della semplice flessibilità: è anche ineguagliabile nelle prestazioni. Il sistema è in grado di accelerare fino a 5 g e raggiunge velocità massime di oltre 4 metri al secondo con un passo del prodotto minimo di soli 50 millimetri. “Quando si combinano questi numeri di prestazioni con i vantaggi dei divertori e l’estrema flessibilità di progettazione, si tratta di un pacchetto totale che il mercato non ha mai visto prima”, afferma l’esperto di meccatronica, fiducioso che l’industria sia all’origine di un salto generazionale nella produttività e ROI accelerato.
Tempo di commercializzazione più rapido
B & R offre una vasta gamma di funzionalità software per far funzionare ACO-POStrak con il minimo dispendio di tempo e fatica. Lo stesso codice applicativo può essere eseguito in simulazione o sull’hardware reale senza limitazioni. “Gli sviluppatori possono passare avanti e indietro tra simulazione e hardware reale tutte le volte necessarie”, spiega Kickinger. Questo breve periodo di sviluppo e di messa in servizio considerevolmente. “Questo è un incredibile vantaggio in termini di time to market”.
Gli sviluppatori beneficiano anche della programmazione orientata ai processi. Descrivono semplicemente le regole che definiscono il flusso del prodotto sulla traccia, piuttosto che dover programmare singolarmente una moltitudine di assi e navette. Il controllo del traffico autonomo con evitamento integrato delle collisioni elimina il lavoro degli sviluppatori.
Personalizzazione di massa
Con ACOPOStrak, B & R ha progettato una soluzione che rende i sistemi di produzione flessibili e modulari altamente redditizi da utilizzare. “Il nostro sistema consente un alto livello