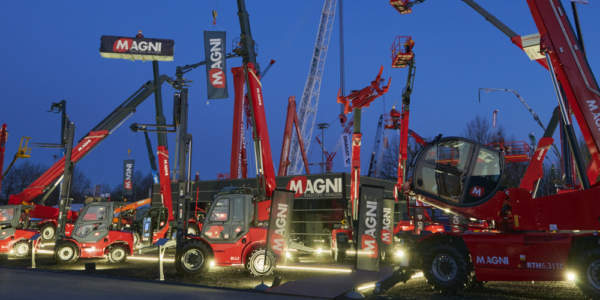
Magni TH, a leading name in the global telescopic handler industry, confirms its participation in Bauma 2025, the world’s foremost exhibition dedicated to construction and lifting equipment. This key event provides the Castelfranco Emilia-based company with an opportunity to showcase its latest innovations: cutting-edge solutions designed to optimise performance, efficiency, and operational safety.
New mid-range TH models: TH 3,5.7 & TH 3,5.9
Magni TH expands its range of fixed telescopic handlers with the launch of the new TH 3,5.7 and TH 3,5.9, two powerful, compact products able to lift up to 3,500 kg and reach heights of 7 and 9 metres respectively. Like all Magni’s other telescopic handlers, these new models are equipped with the Load Moment Indicator (LMI), integrated in the Magni Combi Touch System (MCTS) to guarantee absolute operating safety with any compatible attachment.
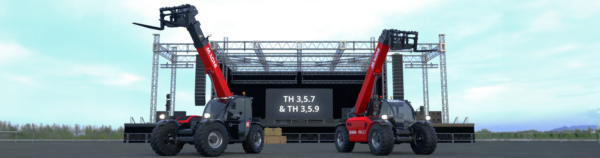
Superior performance and operating versatility
The TH 3,5.7 and TH 3,5.9 models are engineered to handle a wide range of applications, offering exceptional compactness and versatility. Ideal for sectors spanning construction, logistics, and events, they ensure maximum efficiency and safety, even for the most demanding tasks.
One distinctive characteristic of these new models is the cab, derived from the one launched in April 2024 with the model TH 3.6 but more spacious to provide the operator with even greater comfort. Thanks to wide visibility and meticulously designed cab ergonomics, with no detail left to chance, safe, comfortable use is assured during every operation.
The new Magni telescopic handlers are characterised by their compact dimensions: 2 metres high by 2.07 metres wide with length of 4.31 metres with the boom stowed. This is enabled by the dual boom extension system, which allows excellent lifting height without sacrificing agility. These models are ideal even in tight spaces and for jobs in urban contexts or on crowded construction sites.
Advanced technology for superior performance
These two new telescopic handlers are equipped with 75 HP Deutz engine and a hydrostatic transmission which, combined with the Dropbox with two forward and reverse speeds, enables them to cope with gradients of up to 89% and provides a top speed of 32 km/h. The hydraulic pressure of over 300 bar and the sophisticated load sensing system guarantee rapid, fluid, precise motion even when multiple actions are required simultaneously, making these machines ideal for jobs that demand quick, smooth movements.
Safety was fundamental in the design of the TH 3,5.7 and TH 3,5.9 and, as already mentioned, the LMI system supplied as standard ensures constant control in all lifting phases, avoiding the overloads experienced with the usual load cells and above all complete control of the load with all compatible accessories, thus guaranteeing the highest level of safety. Both models will be equipped as standard with 7” touchscreen with the MCTS system, enabling real-time display of the load charts for the attachment being used.
Magni has created two machines that combine outstanding performance, reliability and compact, functional design. Created with a focus on user-friendliness, safety and performance, the new TH 3,5.7 and TH 3,5.9 are destined to rewrite the rulebook in the telescopic handler sector. These models are ready to satisfy the needs of professionals in various sectors and to set the standard for anyone seeking optimal lifting solutions, with absolute safety at all times.
The new RTH 6.31 TC (Tilting cab)
Magni has chosen the Bauma 2025 show floor to unveil its latest tilting cab model, derived from one of the most sought-after rotary telescopic handlers on the global market: the RTH 6.31 TC. This new version joins the elevating and standard cab models already available, offering a lighter and more versatile alternative. Weighing 500 kg less than the elevating cab version, the tilting cab enhances performance and simplifies transport while maintaining efficiency and capability.
The cab tilt can be adjusted via an intuitive dashboard control, allowing the operator to set the trim from 0° to +21°. This system ensures the operator optimal visibility during lifting operations and precise handling during delicate manoeuvres, significantly enhancing comfort, efficiency, and on-site safety.
The “Tilting Cab” range consists of 3 models, including the 31-metre telescopic handler mentioned above, as well as the RTH 6.22 TC and RTH 6.26 TC.
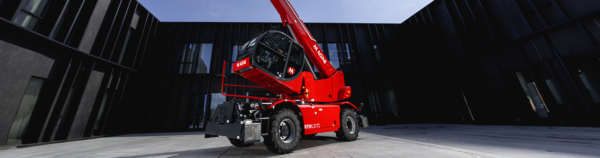
HTH 25.11: sheer power and capacity
The new HTH 25.11 high-capacity telescopic handler is an evolution of the previous HTH 24.11 model, retaining the same dimensions and main technical specifications but with a substantial improvement in load capacity.
One of the main innovations provided by the model HTH 25.11 is the completely revised load chart, which delivers a genuine improvement in performance. With a load capacity of 18,000 kg at the maximum height of 10.5 metres, the new model offers a significant increase over the previous version’s 14,000 kg, with an impressive gain of 4,000 kg at full height (+29%).
The load capacity at maximum horizontal reach of 5.8 m has also been optimised through in-depth research: while the previous model offered a capacity of 7,200 kg, the new HTH 25.11 can lift up to 8,000 kg (+11%), thus ensuring greater operating capacity in even the toughest jobs.
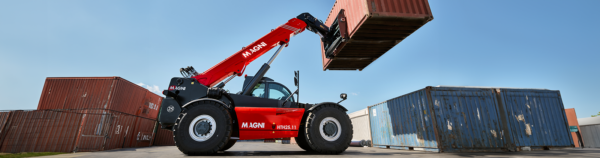
TP 4,5.10 platform: three machines in one
With the introduction of the new TP 4,5.10 platform, Magni rotating telescopic handlers reinforce their status as 3 machines in 1, delivering higher performance than many conventional aerial platforms. This ground-breaking accessory raises the RTH range to an even higher level of efficiency, operating capacity, flexibility and safety.
One of the TP 4,5.10 platform’s most important features is its ability to maintain a constant load capacity of 450 kg (max. 3 occupants) right across the working area, a competitive advantage compared to conventional aerial platforms.
Its innovative rotation system allows the platform to be stowed to the side of the boom, reducing overall dimensions and thus optimising transport. What’s more, the angle correction of +/-20° with boom extended and 360° rotation with boom stowed (max. load capacity 160 kg) improve operating flexibility.
The combination of the RTH 8.46 and TP 4,5.10 sets new standards for Magni work platforms, enabling an overall working height of 58 metres and guaranteeing constant load capacities, state-of-the-art agility and operational compactness.
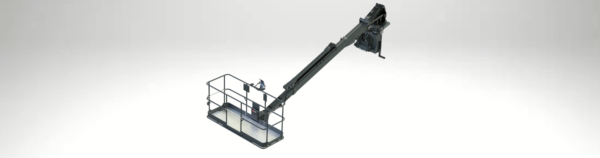
Magni modes for optimising all working needs
M1 – Max Outreach Mode
The RTH boom “Max Outreach Mode”, standard on all Magni rotating telescopic handlers, features a unique extension sequence, with the smaller, end sections extended first and the larger sections kept until last.
This extension mode increases both the range and the load capacity of the boom’s horizontal reach. It also provides greater load capacity at maximum height.
M2 – Max Capacity Mode
The boom extension “Max Capacity Mode” is a leading-edge characteristic provided on RTH 8.35, 8.39 and 8.46 models. It extends the boom sections in a specific order, starting with the largest and finishing with the smallest sections.
This configuration optimises load capacity in the initial phases of boom extension to provide higher capacity than with the “Max Outreach Mode”. This mode is therefore ideal for operations which require lifting of heavy loads within a short operating range.
M3 – Full Power Mode
The new “Full Power Mode” revolutionises the operation of Magni telescopic handlers, deactivating boom extension and retraction when the working position is reached in order to increase load capacity and improve operating stability. Available on 6 and 8 tonne RTH models, in combination with Magni winches or booms with winch this function enables them to rival the performance of off-road cranes in terms of load capacity for a given reach.
This mode allows boom extension to be blocked to reduce the impact of the dynamic forces generated by friction on the chains. In practice, extension is deactivated while rotation and lifting are still enabled, in exactly the same way as on telescopic boom cranes.
The main benefit of this function is the significant increase in load capacity, achieved by eliminating the dynamic effects generated by the boom extension system. What’s more, once these forces have been eliminated the horizontal boom can be extended further, increasing reach capacity.
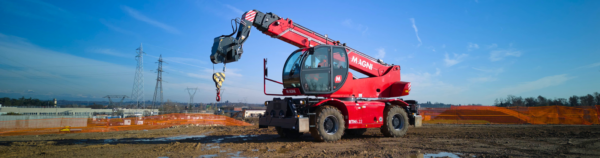
Vertical lift & horizontal placement: absolute precision
Vertical Lift
Vertical Lift is a Magni patented system developed to combine lifting with the telescopic function to ensure perfect vertical lifting. With this state-of-the-art technology, the load is lifted while keeping the machine’s operating radius constant, fundamental in avoiding undesirable deviations or tilting. What’s more, it ensures that the attachment is kept vertical throughout all boom lifting and extension phases, for unrivalled operating stability and precision. The mode must be selected via the MCTS touchscreen, enabling the button on the left side of the joystick. Once the joystick is moved to the lower position, the function can be engaged by manoeuvring it along the longitudinal axis. Vertical Lift revolutionises the world of lifting attachments with a perfect combination of innovation, safety, precision and ease of use.
Horizontal Placement
Horizontal Placement is a new, patented function for Magni telescopic handlers, designed to optimise pallet handling by guaranteeing a perfect, horizontal approach to the unloading point and perfect removal of the forks from the pallets’ fork slots. This function enables more precise control of handling operations and simplifies loading and unloading jobs.
The Horizontal Placement function allows the load to be automatically kept horizontal and levelled throughout the entire set of boom movements, minimising the risk of imbalance or imprecisions. With a single, smooth motion, the system guarantees, for example, that a pallet is placed in the chosen position with the utmost precision, while also facilitating extraction of the forks from the slots.
Horizontal Placement is easily activated: the operator must select the mode on the MCTS touchscreen, enabling the button on the left side of the joystick. Once the joystick is moved to the upper position, the function can be engaged by moving the joystick along the transverse axis. With this dual activation mode, the operator can choose whether to use the joystick button for attachments’ auxiliary functions or to activate the Horizontal Placement procedure.
Thanks to this solution, pallet handling becomes not just faster but also safer, since the technology minimises the risk of errors and improves load stability in all handling phases. This function is particularly useful in environments where precision is fundamental, such as in warehouses and distribution centres.
The Vertical Lift and Horizontal Placement modes are currently available on TH models with a maximum capacity of 4.5 tonnes, and will be progressively introduced across the entire RTH range in the near future.
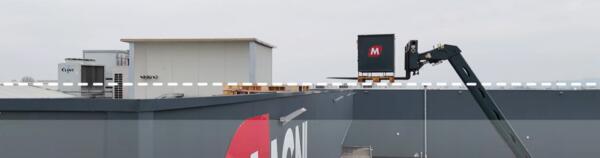
Booster Mode
To accelerate the approach to the load while using the Vertical Lift and Horizontal Placement functions, “Booster Mode” can be activated.
This feature is engaged by pressing the yellow button on the joystick, automatically increasing the speed of boom extension and retraction, even when unloaded, ensuring faster and more efficient operations.
New Forklift models: the FL range
In 2025, Magni will be launching a new FL range of off-road forklifts on the market. These new models will appear alongside the current offering of Magni brand telescopic handlers and lifts.
The initial range will comprise four diesel models with load capacities from 2.5 to 5 tonnes, with 3 metre high-visibility duplex mast as standard. The options of duplex masts from 3.7 to 4 metres or triplex masts from 4 to 5 metres will be available.
Magni forklifts will be distinguished not only by their trademark red colour but also by a basic outfit enhanced by market-specific options to improve safety and operator comfort. Each model will be available in two variants, the first for markets which use Stage V engines and the second, identified by an “A” at the end of the model name, for markets which require Stage IIIA machines. As well as in their engines, the two variants will also differ in a number of features to be provided as standard on the Stage V version, such as the cab with front and rear windscreen and cab working lights.
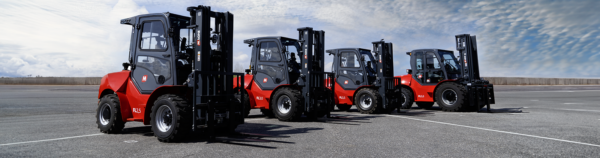
New AC+ Scissor lifts: efficiency and advanced technology
Magni presents the new generation of AC+ scissor lifts, designed to operate on paved surfaces, with load capacity improved by up to 40% compared to the previous models. Working heights vary from 8 to 16 metres, providing greater efficiency thanks to the upgraded lithium battery, which is combined with a new power supply system with high energy efficiency to guarantee longer duration than with conventional batteries.
The gravity energy recovery system recycles energy from the hydraulic fluid during descent to charge the battery by up to 20%, while the electric steering ensures greater reactivity and energy saving of up to 15%. The new high-efficiency drive system has increased the top speed to up to 6 km/h, providing greater productivity and rapid response times.
Integration of the fork slots in the chassis facilitates loading and unloading, improving stability and safety. What’s more, the control panel has been upgraded, with a display three-times larger than the previous generation and silicone buttons. The high- strength tyres, with a new rubber blend and innovative tread pattern, are more wear- resistant, with twice the lifetime of standard tyres.
The system of high-efficiency pumps, with a single pipeline for all the main hydraulic components, reduces the problem of fluid leaks and simplifies maintenance, while the load sensing system with high-precision sensors guarantees accurate monitoring to prevent overloads, with real-time reactivity unaffected by the ambient temperature.