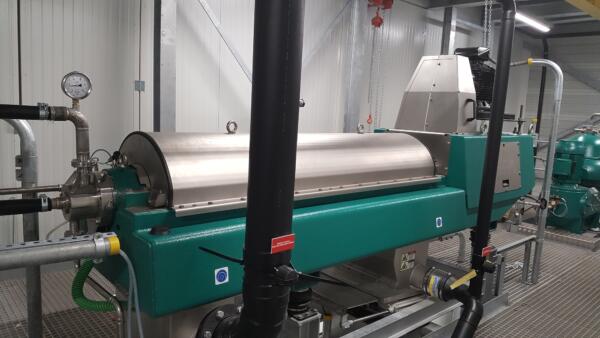
In order to further optimize the product quality of the bio-based raw material Kaumera and to increase product capacity, the Rijn en IJssel water authority as the operator of the Kaumera production plant, and the system provider, machine and plant manufacturer GEA, are working closely together. GEA supplied the centrifuges that are essential to the process of extracting the biopolymer from the Nereda® granular sludge at the Kaumera production plant in Zutphen, the Netherlands.
Kaumera as a real alternative to many materials
The sustainable biopolymer Kaumera is a viable alternative to a wide range of materials, such as petrochemical materials. One of Kaumera’s key properties is its ability to both absorb and repel water. This property offers a wide range of applications in the construction, textile, paper, and concrete industries. In agriculture and horticulture, Kaumera can also reduce the leaching of fertilizers and improve the water storage capacity of crops and soil. Plants can absorb the fertilizer better.
They become more resistant and grow better. Kaumera can also be used as a binder to support the pelletization of powdery materials such as struvite (magnesium-ammonium-phosphate mixture). Kaumera is also a fire retardant. Its water repellent properties make Kaumera a good functional coating for concrete floors. Finally, Kaumera can also be combined with other raw materials to form composite materials.
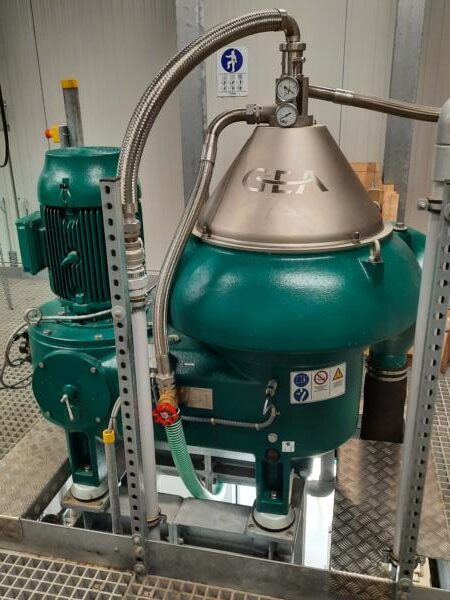
Close cooperation at eye level
Developing a sustainable product like Kaumera requires partners with a great deal of expertise and experience. Mark Smit is R&D Engineer/Manager Operations at the Rijn en IJssel water authority. He is enthusiastic about the collaboration between the two companies. “GEA’s vision and consistent implementation are well aligned with our sustainability goals and those of the water authority. We are looking for new ways to extract valuable, bio-based raw materials and other components from the treatment process and to recycle them”, Smit adds: “In this way, we produce cleaner water, reduce our carbon footprint and create added value from streams that were previously considered waste. That’s what Kaumera is all about.“
“The last process step is crucial”
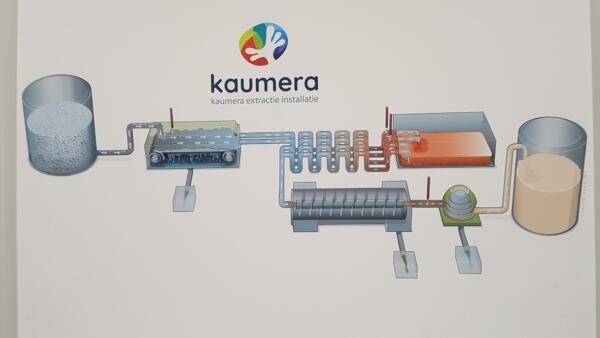
Dr. Birte Clason works as Senior Process Engineer for the Business Line Environment in the Business Unit Separators at GEA. She has been part of the project team since 2017, working closely with Kaumera. “We are supplying the mechanical treatment in the process for Kaumera. In particular, the last two process steps in the decanter and disk centrifuge are crucial for Kaumera’s quality. We have worked a lot on this step in recent years to find out how we can optimize it. In close cooperation with our customer, we want to continue to consistently improve the quality of Kaumera.” She praises the collaboration with the water authority. “The special thing about the cooperation is that the discussions are always open and based on trust. Together we have found solutions and removed obstacles.”
A few examples: During the installation, commissioning, and process optimization of the GEA systems in the production in Zutphen, the water authority and GEA employees were on site several times. This meant that changes could be tested directly in Zutphen and the results discussed immediately. “It is a very fruitful collaboration in which we help each other and everyone contributes their knowledge and experience” says Birte Clason.
Looking to the future
“Any adjustment we want to make to the process has a direct impact on GEA’s modern equipment” explains Mark Smit. “The team at GEA strives to find the best technical solutions, even when there are challenges. It’s not always the easiest way, but it’s the way to find lasting and sustainable solutions.” For example, GEA is improving Kaumera’s product quality by making various technical modifications to the two centrifuges. “Comprehensive figures from production and their analysis provide a wealth of knowledge. Together with GEA, we are gaining extensive knowledge about the Kaumera extraction technology that we may be able to apply worldwide” says Smit. And it goes even further and bigger. “During our meetings, we also develop new ideas that benefit not only Kaumera but the entire water treatment industry. Who knows what the future will bring if we continue to pool our expertise” says Smit, looking ahead.